Combustion Efficiency and Excess Air
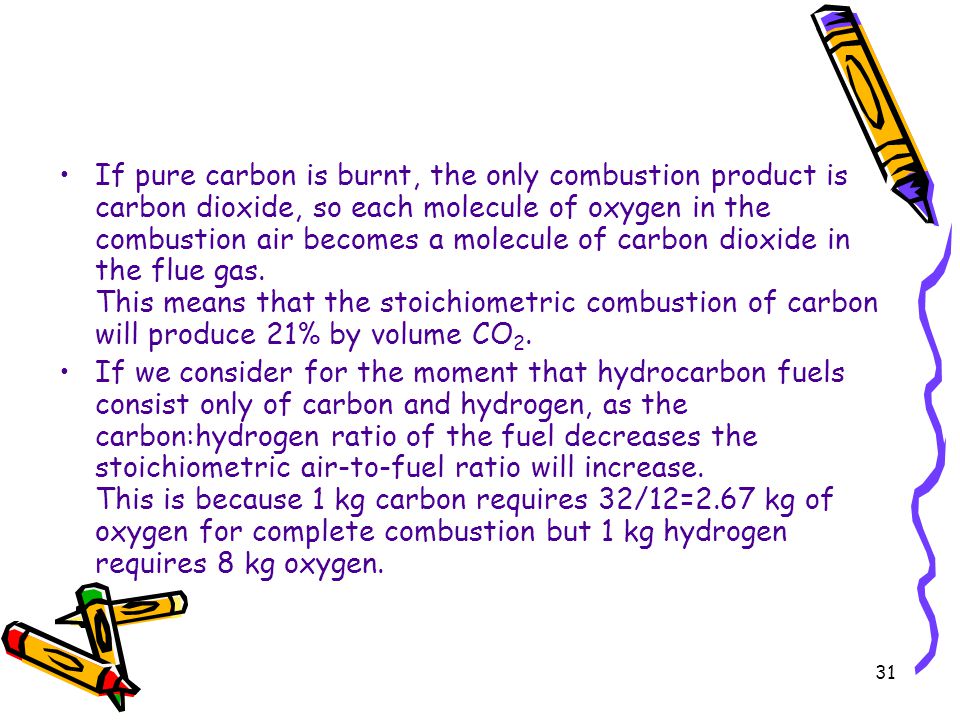
Optimizing boilers efficiency is important to minimize fuel consumption and unwanted excess to the environment
To ensure complete combustion of the fuel used combustion chambers are supplied with excess air. Excess air increase the amount of oxygen to the combustion and the combustion of fuel.
- when fuel and oxygen from the air are in perfect balance - the combustion is said to be stoichiometric
The combustion efficiency increases with increased excess air - until the heat loss in the excess air is larger than the heat provided by more efficient combustion.

Excess air to achieve highest possible efficiency for some common fuels:
- 5 - 10% for natural gas
- 5 - 20% for fuel oil
- 15 - 60% for coal
Carbon dioxide - CO2 - is a combustion product and the content of CO2 in a flue gas is an important indication of the combustion efficiency.
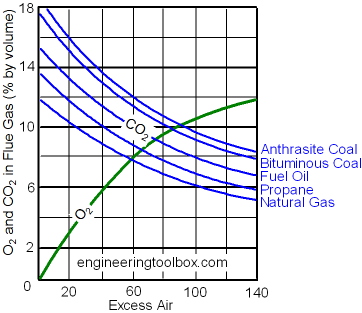
Optimal content of carbon dioxide - CO2 - after combustion is approximately 10% for natural gas and approximately 13% for lighter oils.
Normal combustion efficiency for natural gas at different combinations of excess air and flue gas temperatures are indicated below:
Combustion Efficiency (%) | ||||||
---|---|---|---|---|---|---|
Excess (%) | Net Stack Temperature1) (oF) | |||||
Air | Oxygen | 200 | 300 | 400 | 500 | 600 |
9.5 | 2.0 | 85.4 | 83.1 | 80.8 | 78.4 | 76.0 |
15 | 3.0 | 85.2 | 82.8 | 80.4 | 77.9 | 75.4 |
28.1 | 5.0 | 84.7 | 82.1 | 79.5 | 76.7 | 74.0 |
44.9 | 7.0 | 84.1 | 81.2 | 78.2 | 75.2 | 72.1 |
81.6 | 10.0 | 82.8 | 79.3 | 75.6 | 71.9 | 68.2 |
1) "Net stack temperature" is temperature difference between flue gas temperature inside the chimney and room temperature outside the burner.
Flue Gas Loss with Oil Combustion
The relation between temperature difference in flue gas and supply air, the CO2 concentration in the flue gas, and the efficiency loss in the flue gas oil combustion, is expressed below:
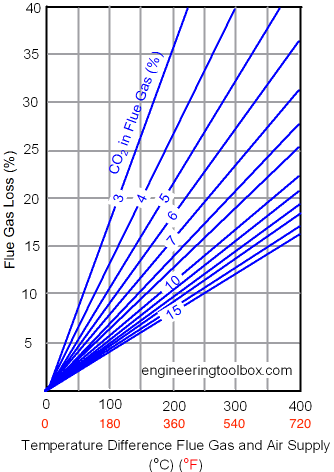
Example - Oil Combustion and Heat Loss in the Flue Gas
If
- the temperature difference between the flue gas leaving a boiler and the ambient supply temperature is 300 oC, and
- the carbon dioxide measured in the flue gas is 10% - then,
from the diagram above
- the flue gas loss can be estimated to approximately 16%.
All combustion processes require the correct oxygen to fuel ratio as it directly effects boiler efficiency. Too little oxygen results in incomplete combustion creating harmful emissions. Setting the boiler to burn with excess oxygen is the normal solution to reducing emissions. SST’s Zirconium Dioxide oxygen sensors can help customers optimise their boiler combustion efficiency within the oil, coal, gas and biomass boiler market.
Results of incorrect combustion include fuel waste, an increased level of toxic emissions and potentially damaging the combustion system. Environmental and financial impacts can be significant.
The overheads of fuel consumption and system value are high in large scale industrial and commercial boilers/furnaces. In order to see return of investment and minimal running costs the operation must be kept at peak efficiency.
Complete combustion requires the correct ratio of fuel and oxygen. This is optimised and maintained by measuring the output of oxygen level of the exhaust/flue gas by using an oxygen sensor in a closed loop feedback system to a controller for regulating the input mix. This is especially useful when the quality of fuel supplied may vary (i.e. gas from different sources).

SST’s zirconium dioxide oxygen sensors help customers to optimise their boiler combustion efficiency within the oil, coal, gas and biomass boiler market. The oxygen sensors have been used to provide a clean burn and reduce harmful emissions in combustion processes for over 25 years. The oxygen sensor is inserted into the boiler flue to monitor the oxygen level, enabling complete control over the boilers oxygen to fuel ratio.
Here is an example of a combustion process using SST’s zirconium dioxide oxygen analyser, the OXY-Flex as a feedback signal into the controller system. The diagram illustrates boiler combustion efficiency and emissions against the air to fuel ratio.
SST’s sensors allow the excess oxygen to be reduced while still maintaining safe operation. This saves both money and the environment.
SST’s zirconium dioxide oxygen sensors come stand-alone or with integrated electronics, like our OXY-Flex oxygen analyser, offering digital or analogue industry standard outputs.
Their long life comes from their non-depleting sensor cell technology. No reference gas is required and easy single point calibration can be performed in fresh air or any other known oxygen concentration. The sensors offer an accurate and selectable measuring range (0.1 to 25% O₂ or 0.1 to 100% O₂), a fast response time from as little as four seconds and are RoHS compliant. Their stainless steel construction gives them the ability to function in combustion processes with extreme operating temperatures (up to 400⁰C), resulting in a rugged, robust, reliable and ready to use solution.
Air Fuel Ratio Effect Combustion Efficiency and Air Fuel Ratio
In part two of this series on combustion control of industrial heat sources, we consider the air fuel ratio and the balance of using excess air to consume combustibles while minimizing energy from going up the stack in industrial heating sources. In Part I, Stoichiometric Combustion and its Impact on Boiler Efficiency, we discussed stoichiometric combustion, that theoretical position in which the optimal amount of oxygen and fuel mixture, to produce the most heat possible while achieving maximum combustion efficiency.
Air Fuel Ratio and Excess Air
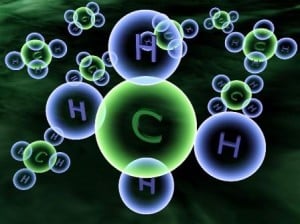
In fuel-fired process heating, the largest source of energy loss is through the exhaust stack, which is why managing air flow is essential to combustion efficiency. When fuel burns in the presence of oxygen it is converted to carbon dioxide, water and heat. Consider the combustion of methane (CH4).
CH4 + 2O2 → CO2 + 2H2O + Heat (1,013 Btu/ft.3)
Air contains approximately 21% oxygen and 79% nitrogen. In this case the reaction for complete combustion becomes:
CH4 + 2O2 + 7.53N2→ CO2 + 2H2O + 7.53 N2 + Heat (1,013 Btu/ft.3)
The amount of air required will vary depending on the type of fuel. Ideally you would like to add enough oxygen to consume all the fuel so that little or no combustibles are exhausted while minimizing the excess air to prevent energy loss out of the stack.
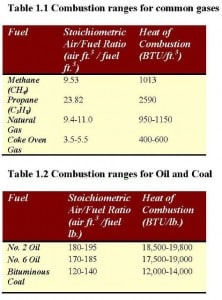
Air-to-fuel ratio defines the amount of air needed to burn a specific fuel. The conventional fuels used in a combustion process are: oil (#2, 4 and 6), diesel oil, gasoline, natural gas, propane, and wood. Ratios for common gases, liquid and solid fuels are noted on Table 1.1 and 1.2.
Optimizing Air-to-Fuel Ratio
For any combustion process there is a balance sought between losing energy from using too much air, and wasting energy from running too richly. The best combustion efficiency occurs at the optimum air-to-fuel ratio and controlling this provides the highest efficiency. In most scenarios, a liquid and gas fuel burner achieves this desired balance by operating at 105% to 120% of the optimal theoretical air. For natural gas fired burners, the stoichiometric air required is 9.4-11 ft.3 / 1.0 ft.3 of natural gas, or approximately an air-to-gas ratio of approximately 10:1. This results in an excess oxygen level of 2%.
In the combustion zone, it is difficult to measure excess air. In the stack, however, it can be easily measured using Oxygen analyzers. When operating with 5%-20% excess air, it would correspond to a 1% to 3% oxygen measurement in the stack.
The ideal air-to-fuel relationship will vary at different operating loads. Tuning is the act of establishing the desired air-to-fuel relationship under different operating conditions. This can be accomplished when evaluating specifics in the stack: temperature, oxygen concentration, as well as carbon monoxide and NOx emissions.
In part three of this five-part series on combustion control, we consider analyzing flue gas oxygen and combustibles, along with varying air, and fuel pre-combustion flows to improve combustion efficiency of industrial boilers, steam generators, furnaces, ovens, smelters and process heaters.
No comments:
Post a Comment