Measuring Viscosity with Onsite Viscometers
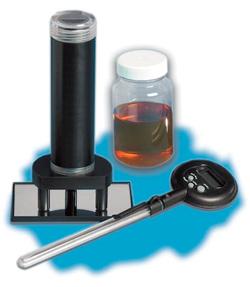
Because the viscosity of an oil is probably its single most important property, it makes sense to measure viscosity frequently, using onsite test equipment. However, like all onsite equipment, it’s important to understand how these instruments work and their relative strengths and weaknesses.
When it comes to viscosity, there are two determinable parameters — absolute and kinematic viscosity. Kinematic viscosity measures the resistance of an oil to flow and shear under gravity, such as oil flowing through a funnel. Absolute viscosity, on the other hand, determines an oil’s internal resistance to flow and shear. To visualize absolute viscosity, imagine the force needed to stir an oil using a metal rod.
The viscosity reported by your lube supplier and oil analysis lab is likely the kinematic viscosity. There are two main reasons why your onsite measurements may not correlate directly with the lab data.
First, most onsite test equipment actually measures absolute viscosity, but calculates the kinematic viscosity by dividing absolute viscosity by density. Because the onsite viscometers don’t actually measure density but rather estimate it from the oil’s spec sheets, an error can occur when translating absolute viscosity into kinematic viscosity. The measure of the absolute viscosity is correct, but because the density of the oil is only estimated, the conversion to kinematic viscosity can become overstated. Contamination and oxidation, among other things, can cause a rise in the density of used oil.
Second, if your onsite instrument does not heat the oil to 40 degrees C, and most do not, you are likely determining the oil’s viscosity at the temperature of the onsite lab (typically in the 20 to 25 degrees C range), and extrapolating, again using a software algorithm to determine the viscosity at 40 degrees C. This extrapolation can also introduce errors into the reported measurement due to changes in viscosity index of the used oil.
Despite these limitations (which actually are not negatives), used properly, onsite viscometers make very valuable additions to any onsite test program. As a general rule, always baseline your new oils using your own onsite viscometer to determine nonconforming used oil viscosities quickly and simply.
No comments:
Post a Comment