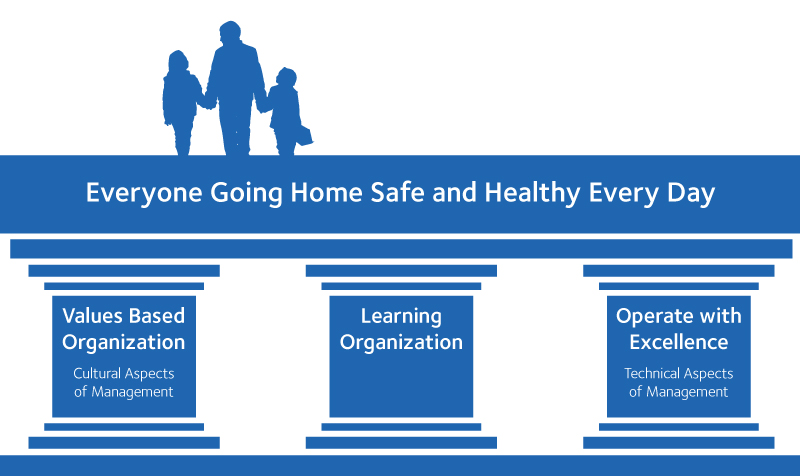
SITE IN-CHARGE SHRI GVS ANAND SIR FOCUSED ON THE THEME AND APPEAL TO ALL FOLLOW SAFETY AS CULTURE.
AND SHRI MV SIVA KUMAR REDDY SIR BRIEFED ABOUT THE THEME AND REQUEST TO ALL MUST ACHIEVE IT .


Many safety managers think they have solved all safety issues by being compliant with government, insurance and corporate mandates. The truth is: these companies are not only at risk, but are most likely still incredibly inefficient in their safety processes. Aberdeen’s ongoing research into safety and operational performance shows that leading manufacturing companies do three specific things to build an efficient safety culture:
- Establish an effective continuous improvement program around safety processes.
- Automate processes like Job Hazard Analysis (JHA) and incident management as much as possible.
- Use continuous improvement techniques and analytical techniques to connect JHA to incident management and optimize your JHA by monitoring incident management.
A recent Aberdeen study on the Environment, Health, and Safety (EH&S) side of manufacturing found that EH&S affects all levels of an organization, from plant manager to CEO. Getting buy-in from these various levels of the company is crucial, as that is where a safety culture comes in. However, this focus on safety should go beyond compliance and work to reduce manufacturing costs and increase productivity. Organizations looking to develop or improve the safety culture in their own company should:
- Establish standardized policies to minimize risk of business interruption due to EH&S events.
- Establish cross-functional teams to bring knowledge and viewpoints from multiple business areas and get everyone thinking about safety.
- Make your business process auditable and transparent for all functional groups. This shares needed compliance information among employees, suppliers, customers, and regulators.
- Automate your safety processes through a formal safety management system (SMS), which eliminates inefficient manual data collection and spreadsheet analysis.
- Use job hazard analysis (JHA) and incident management as the foundation for continuous improvement feedback loops.
- Utilize analytics to identify new trends from behavioral analysis and simplify complex decision making.
- This is not a one-time program. It is a continuous loop that should be driven by a continuous improvement culture and further refined and enha

Understanding the 7 attributes
Shared awareness of the most significant risks
There is a shared awareness of the most significant risks, beyond minor accidents. Risk analyses involve operational staff and their results are widely shared. Employees are regularly reminded of the possibility of serious accidents, in order to reduce fatalism (if they do occur, it won’t be due to a “stroke of bad luck”).
Questioning attitude
There is a shared conviction that risks are never fully managed. Doubt is valued. Vigilance is shared by all operational staff at all times.
Integrated culture, everyone is mobilised
The organisation acknowledges that no single person has all the information and knowledge necessary to ensure safety. Safety requires a commitment from senior executives, managers, and employees in both operational and support departments (HSE, HR, engineering, procurement, etc.). Each person participates in safety by following the rules, and making a proactive contribution (reporting incidents, making suggestions).
Right balance between rule-based and managed safety
The organisation prepares itself both for events that it is able to anticipate and for those it is not.
Predictable events are the topic of group discussions involving operational teams, and the focus of regular drills.
Constant attention to the three pillars
The technical barriers that are defined during the design stage are compatible with production and maintenance operations. They are regularly maintained and updated.
Management leadership and employee involvement
Safety is taken into account in all decisions.
When it comes to safety, management adopts a directive-participative approach to leadership that encourages compliance and proactiveness.
Debates between professionals concerning safe work practices are encouraged.
Culture of transparency
Managerial practices encourage trust and foster a speak-up climate. Top management ensures that words (company statements) and actions (company decisions) are aligned. Information flow is encouraged.
There is a shared awareness of the most significant risks, beyond minor accidents. Risk analyses involve operational staff and their results are widely shared. Employees are regularly reminded of the possibility of serious accidents, in order to reduce fatalism (if they do occur, it won’t be due to a “stroke of bad luck”).
Questioning attitude
There is a shared conviction that risks are never fully managed. Doubt is valued. Vigilance is shared by all operational staff at all times.
Integrated culture, everyone is mobilised
The organisation acknowledges that no single person has all the information and knowledge necessary to ensure safety. Safety requires a commitment from senior executives, managers, and employees in both operational and support departments (HSE, HR, engineering, procurement, etc.). Each person participates in safety by following the rules, and making a proactive contribution (reporting incidents, making suggestions).
Right balance between rule-based and managed safety
The organisation prepares itself both for events that it is able to anticipate and for those it is not.
Predictable events are the topic of group discussions involving operational teams, and the focus of regular drills.
Constant attention to the three pillars
The technical barriers that are defined during the design stage are compatible with production and maintenance operations. They are regularly maintained and updated.
Management leadership and employee involvement
Safety is taken into account in all decisions.
When it comes to safety, management adopts a directive-participative approach to leadership that encourages compliance and proactiveness.
Debates between professionals concerning safe work practices are encouraged.
Culture of transparency
Managerial practices encourage trust and foster a speak-up climate. Top management ensures that words (company statements) and actions (company decisions) are aligned. Information flow is encouraged.
No comments:
Post a Comment