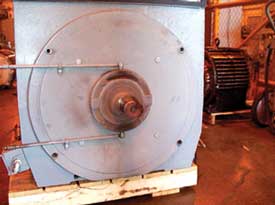
Photo 1. The huge motor in question at
the Eastman Chemical plant.
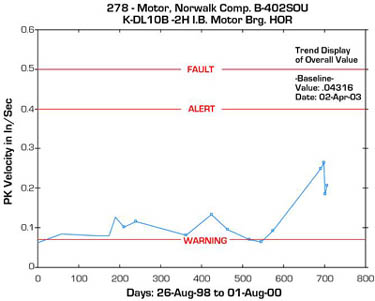
Photo 1. The huge motor in question at the Eastman Chemical plant.
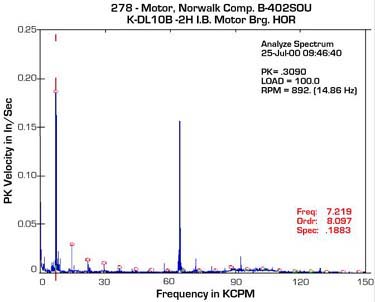
Graph 2. Analysis of the motor outbound bearing spectrum.
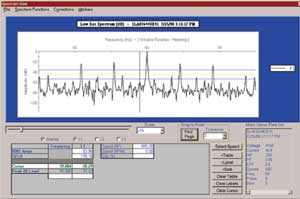
Graph 3. Current analysis readings for the subject motor.
Don’t Stop Here
Many times, our reliability groups want to stop at this point and claim the savings for preventing an unplanned outage or catastrophic failure. But to obtain a greater benefit from our condition-monitoring technologies, we must take the next step.
Our motor analysis team followed the subject motor to our local motor repair shop to verify the bearing problem and try to determine the causes of this problem. Upon removing the grease fill and discharge tubes, the team noted that the grease in the fill tube was not our specified grease for motors. The fill tube contained Interlube Red Hi-Lo grease, where our specified motor grease was Exxon Polyrex EM (Photo 2).
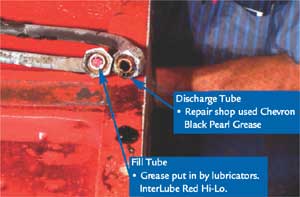
Photo 2. Analysis of fill and discharge
tubes reveals problems.
It was also noted that we were using a spherical roller bearing in a belt drive application. A decision was made to change the bearing to a cylindrical roller bearing to increase the radial load capacity.
Don’t Stop Here Either
Many times our reliability groups are tempted to stop at this point, and we pat ourselves on the back and claim our problem solved by correcting the bearing and grease specification on the subject motor. But to obtain the greatest benefit from our condition-monitoring technologies, we must take the next step. We must identify the system or latent cause of the failure and address these causes to gain the most benefit for our company. How did the wrong greases get into this bearing? Are there other motors in this area or in the plant that are receiving non-specified greases? Why is the motor repair shop using something other than the grease we specified for our motors within the plant?
Some of the other actions that were taken as a result of the findings and subsequent root cause analysis were:
-
Findings were communicated to our Lubrication Services Group to
insure that the subject grease was not being used in other applications.
Although we no longer specified this grease on any plant equipment, it
was determined that many of the lubricators still had an inventory of
this grease in their areas. The Interlube Red Hi-Lo grease was removed
from all lubrication storage areas.
-
The Lubrication Services Group had changed the grease specification
within the plant, but this had not been communicated to the affected
service providers. A meeting was held with our motor repair shop to
communicate our findings, the result of mixing incompatible greases and
our expectations for the future.
-
A new repair specification was developed as a result of this and
several other significant motor failures. The grease specification was
included in the repair specification. The previous repair specification
did not include a grease specification.
-
As a result of these findings and findings on several other motors, a
decision was made to develop a motor repair evaluation process and
team.
This case illustrates the extra benefits of taking your condition-monitoring program to the next level. By becoming more proactive and taking the next step when identifying problems with condition- monitoring technologies, you can determine the system or latent cause and apply the subsequent solution and/or learnings throughout the plant.
No comments:
Post a Comment