Compressors: Time for an oil change?
Lubricating oils developed specifically for ammonia refrigeration compressors can enhance reliability and reduce operating costs as Nick McDonald, market development officer of Kluber Lubrication GB explains

DURING recent years there have been an increasing number of problems with the lubrication of ammonia refrigeration compressors, which have affected the reliability and efficiency of the entire refrigeration plant. On the one hand, the lubricating oil has to meet higher demands: oil-fill quantities have been reduced while temperature, pressure and speed have increased.
Moreover, plant operators are trying to achieve extended maintenance intervals to reduce costs. On the other hand, the oils in use (mainly naphthenic mineral oils) are not always in a position to meet these requirements. However, today there are specially developed lubricating oils available, which fulfil the above requirements and assist in the prevention of potential problems.
Black oil and residue formation
The intense contact between the ammonia and the lubricating oil in refrigeration compressors constitutes a great challenge. The unsaturated hydrocarbons and the sulphur compounds contained in mineral oils may react with the aggressive refrigerant ammonia. Due to this chemical reaction the oil gradually becomes darker until, eventually, it turns black.
The reaction products, which are insoluble in the oil, remain in the compressor or the refrigeration cycle (mainly in the evaporator and the condenser) as residues or sludge. These residues may bring down refrigeration plant efficiency (due to reduced heat transfer in the heat exchangers) and noticeably affect operational reliability. Experience shows that blackening and acidification of the oil can be accelerated in particular by the presence of air and water in the refrigeration cycle (up to 3% of water is possible). In addition to that, abrasive wear caused by oil sludge may directly attack various compressor components. Also, the oil filter and separator are under increased strain and are more susceptible to clogging. All this leads to a reduced lifetime of the components, a drop in efficiency and increased operating costs.
A solution can be found in the use of hydrogenated mineral oils or synthetic lubricating oils.
Klüber has taken the mineral oil route with Klüber Summit RHT-68, a paraffinic, hydrogenated mineral oil developed for use on ammonia refrigeration plants with evaporator temperatures down to -36ºC. The hydrogenation of the base oil (also called hydrotreating) removes unsaturated and sulphur compounds from the oil. Thus, the oil is being cleaned and becomes less reactive with ammonia. Changing from a naphthenic mineral oil to this type of oil constitutes no problem at all. The same goes for Klüber Summit RPA-68, a fully synthetic lubricating oil based on polyalphaolefine (PAO) and alkylbenzene. This oil was developed especially for low evaporator temperatures down to -55ºC when, due to their high pour point, mineral oils are no longer capable of flowing. Finally, Klüber Summit R-200, is not only suitable for use with ammonia, but can also be applied in combination with CO2, propane or butane. As a fully synthetic polyalphaolefine lubricating oil, it is NSF registered for use in the food processing industry and is suitable for evaporator temperatures down to -55ºC.
Both synthetic products contain very chemically-stable base oils. Their high resistance to reaction with ammonia prevents blackening of the oils, a phenomenon that is very common with conventional mineral oils, and undesirable residue formation in the evaporator.
High oil consumption of the compressor
The quantity of oil carried over from the compression chamber into the refrigeration cycle, the so-called oil carry-over, depends, among others, on the evaporation tendency (vapour pressure) of the oil at the relevant discharge temperature (sometimes clearly above 100ºC).
A high oil carry-over, caused by the comparatively high evaporation rate of a naphthenic mineral oil, may lead to excessive oil consumption and increased maintenance requirements due to frequent oil top-up. Both phenomena lead to increased operating costs.
Here, too, hydrogenated or fully synthetic oils offer a satisfactory solution: highly refined, chemically-stable base oils clearly reduce oil carry-over as compared to conventional mineral oils, thus contributing to a reduction in oil consumption of the compressor.
A practical example illustrates the potential savings: a refrigeration compressor charged with 200 litres of mineral oil operated for around 7,000 service hours per year. The operator had to replenish around 300 litres of oil per year, about 1.5 times the filling quantity. When changing to a hydrogenated mineral oil, the refill quantity was reduced by up to 70%.
Reduced oil change intervals
As it is the low-molecular constituents of the mineral oil which evaporate the fastest in the compression chamber, oil viscosity gradually increases over a period of time. Apart from the viscosity increase, blackening of the oil and sludge and residue formation may be other reasons for excessive ageing of the oil. All this inevitably leads to frequent oil changes, which interrupt normal operation and can be very costly. Highly refined and specially formulated mineral and synthetic oils do not contain these volatile oil constituents.
Therefore, oil viscosity remains stable over a long period of time, permitting oil change intervals of up to four or five times longer. The operator of a refrigeration compressor, which was lubricated with naphthenic oil (ISO VG 68), measured a viscosity increase of the oil from 68 to 105mm2/s after only 2,000 service hours. Changing over to synthetic oil enabled him to extend oil lifetime to six times that of the mineral oil fill.
Compatibility with seals
Despite the undeniable advantages offered by synthetic oils, there is still a lot of uncertainty regarding changeover to these oils, with concerns for compatibility with seals for example. Naphthenic oils often cause seals to swell, while some synthetic oils (in particular PAOs) have the contrary effect and may lead to seal shrinkage. In ammonia refrigeration compressors in particular, where neoprene seals are often used, leakage may occur following changeover from a naphthenic lubricating oil to a polyalphaolefine.
In this instance, Klüber Lubrication offers a special oil, which considerably simplifies changeover: a polyalphaolefine mixed with alkylbenzene, where the shrinking effect of one constituent is neutralised by the swelling effect of the other, achieving a neutral behaviour towards sealing materials.
Greater care has to be taken when changing from a naphthenic oil to a pure PAO with seal shrinking effect. Pure PAOs, such as Klüber Summit R 200 may cause a seal which has swollen in contact with the naphtenic oil to shrink, which may lead to leakage at O-rings in the housing or at face and shaft sealing rings. When changing over to Klüber Summit R 200 (one reason to choose this product may be its NSF approval for the food processing industry), operators are advised to renew any O-rings, face seals or shaft sealing rings.
Oil changeover
Klüber Lubrication offers tailor-made lubricants for refrigeration compressor and, on request, also provides support for oil changeover. The first step consists of a detailed oil analysis of the oil presently used, which gives an indication as to the current state of the refrigeration plant and may highlight “hidden” problems. Once the best solution for the particular customer has been determined, a service team can assist in the oil changeover on the plant.
The procedure depends largely on the degree of oil contamination and/or the compressor. Usually it is sufficient to simply drain the oil, replace filters and oil separators and to remove any residual oil from the pipes, housings and filters before filling with the new oil. For heavily contaminated screw compressors, Klüber offers an oil-based cleaning concentrate which is added to the compressor oil in a 10% concentration 60 hours before the planned oil change.
The compressor continues to operate during these 60 hours, and residues and deposits are dissolved by the cleaning agent. The compressor does not have to be dismantled for cleaning.
Also, after the changeover to new oil, Klüber Lubrication can provide further support. Together with the customer, Klüber lubrication’s specialists can inspect used oil samples at regular intervals. Should any problems occur, the situation is analysed and counter measures can be taken immediately. Always, the objective is to reduce maintenance costs and achieve the best possible availability and reliability of a refrigeration plant.
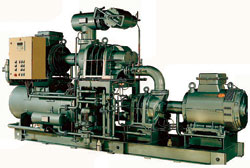
Changing over from naphthenic mineral oils to the new generation of hydrogenated mineral oils and fully synthetic lubricating oils offers many advantages. In many cases, these lubricants enable untroubled and reliable operation of refrigeration compressors without frequent interruptions due to unavoidable cleaning or maintenance. Worn parts are replaced less frequently and filter costs are reduced. Oil change intervals, on the other hand, are noticeably extended by up to six times longer and oil consumption decreased by as much as 70%.
And last but not least, due to the absence of oil-related residues, the efficiency of the refrigeration plant as a whole should increase. A successful changeover, however, requires a high degree of experience and know-how. Therefore, a competent oil supplier should advise the customer, provide a tailor-made solution and support them during the entire changeover period.
BVA
717P AMMONIA Oil
BVA
717P is a specially designed lubricant for use in ammonia
refrigeration systems. It is a highly
stable fluid,
specially formulated so that it does not react with ammonia.
The technology used in this fluid is used by many OEM refrigeration
system manufacturers as their factory & service fluids.
BVA 717P specialized formulation, together with it's two
stage hydrocracked base stocks, gives it excellent oxidation
resistance, high viscosity, film strength at operating
temperatures, fast separation from ammonia and excellent
demiscibility. BVA 717P almost colorless appearance, low volatility and almost complete absence of aromatics and high flash point contribute to safer operation of plant refrigeration equipment. BVA717P ammonia refrigeration fluid is recommended for all compressor lubricants in ammonia refrigeration systems. It's non sludging and oxidation resistant properties make it the perfect choice for ammonia systems. |
![]() Sub Categories |
TYPICAL SPECS | BVA 717P-68 |
Viscosity
at 100 ° F SUS Viscosity at 210 ° F SUS Viscosity at 40 °C cSt Viscosity Index Flash Point ° F COC Pour Point ° F Di Electric KV Specific Gravity @ 60° F |
300
53 64 97 440 - 36 35 0.86 |
No comments:
Post a Comment