The OSHA Laboratory Standard
A comprehensive summary of the significant provisions of the regulation
In 1990, the Occupational Safety and Health Administration (OSHA) promulgated the regulation "Occupational Exposures to Hazardous Chemicals in Laboratories," 29 CFR 1910.1450. This regulation, commonly known as the Laboratory Standard, was designed to ensure that laboratory workers are informed about the physical and chemical hazards of chemicals in their workplace and are protected from chemical exposures exceeding allowable levels.
For a laboratory to be governed by the standard, the lab must meet specific criteria. Covered under the rule are workplaces that use relatively small quantities of hazardous chemicals. Multiple chemical procedures or chemicals are used, and the procedures involved are not part of a production process. These laboratories must use or handle hazardous chemicals and manipulate them on a “laboratory scale” basis.
This article provides a comprehensive summary of the significant provisions of the regulation. In promulgating this standard, OSHA placed primary emphasis on administrative controls to lessen the threat of overexposure to hazardous substances in laboratories.
Administrative controls
Administrative controls consist of various hazard control requirements that are established at a managerial level by an appropriate individual or group (e.g., laboratory manager, laboratory supervisor, or safety committee) to promote safety in the laboratory. Administrative controls do not remove hazards, but reduce or prevent exposure to them. Some common examples of administrative controls include written plans and procedural controls (e.g., safe work practices and standard operating procedures), training and information, exposure monitoring, medical examinations, hazard identification, and record keeping.
For those people who have the primary responsibility for maintaining laboratories under their supervision, the Laboratory Standard consists of the following major elements:
- Exposure monitoring
- Chemical hygiene plan
- Employee information and training
- Medical consultation and medical examinations
- Hazard identification
- Use of respirators
- Record keeping
Exposure monitoring
For laboratory uses of chemicals that are regulated in 29 CFR 1910.1000, subpart Z, the employer must ensure that laboratory workers are not exposed to these chemicals above their respective permissible exposure limits (PELs). The employee must measure the worker's exposure to any chemical regulated by a standard, which contains exposure monitoring and medical surveillance requirements if there is reason to believe that exposure levels for that chemical routinely exceed the action level, or in the absence of an action level, the PEL.
If initial monitoring discloses employee exposure above the action level (or PEL, where no action level exists), the employer must immediately comply with the exposure monitoring provisions of the relevant standard. Monitoring may be terminated as prescribed by that standard. Any exposure monitoring results obtained must be provided in writing to affected laboratory staff within 15 working days after the receipt of the results.
Chemical hygiene plan (CHP)
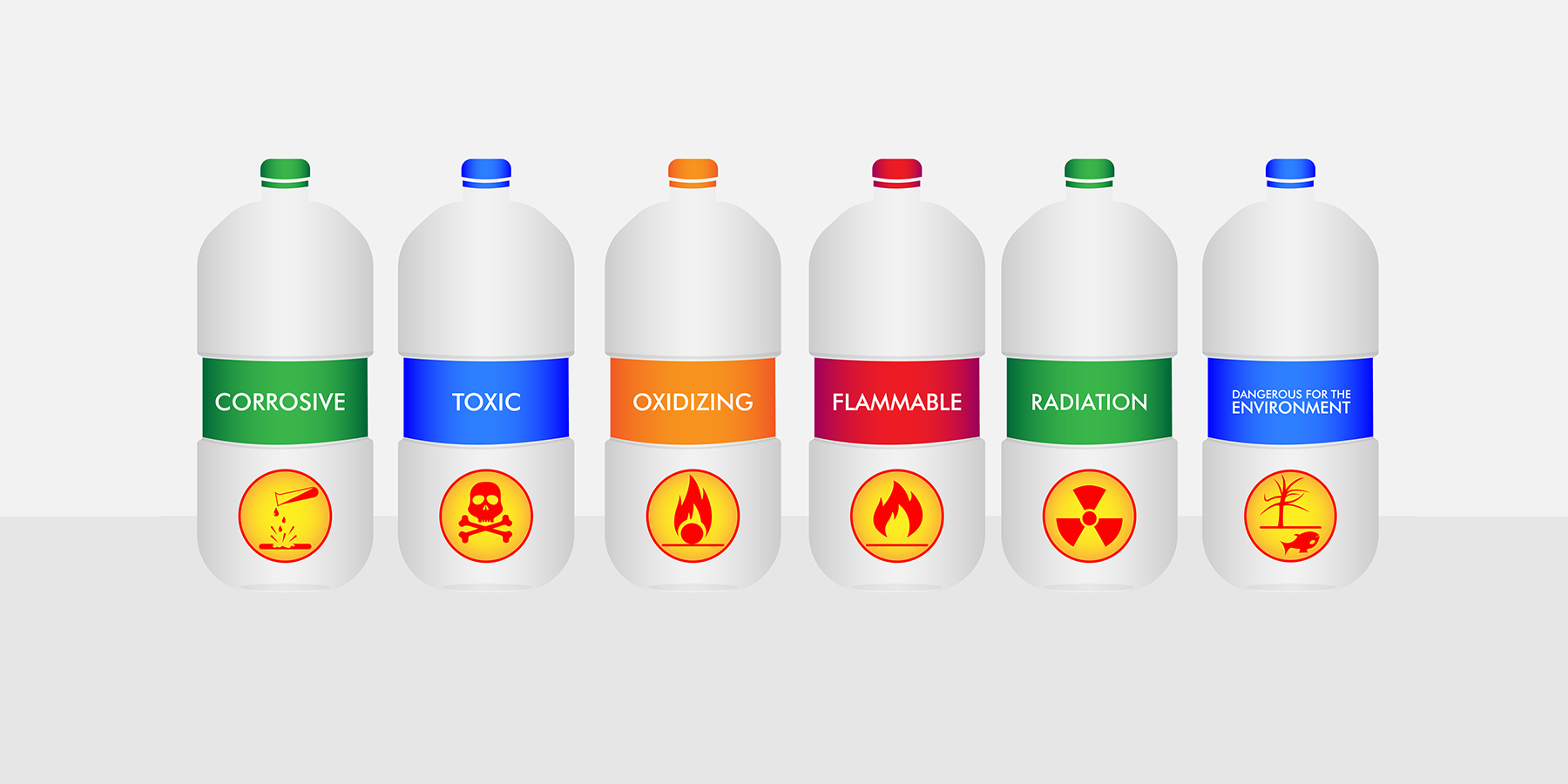
ISTOCK
The heart of the laboratory standard is the chemical hygiene plan (CHP). The regulation requires the employer to create and implement a written plan or program that is capable of protecting laboratory employees from the health hazards associated with the chemicals with which they work. The plan must include the necessary procedures, work practices, training, designation of a chemical hygiene officer, medical consultation and examinations, exposure monitoring, engineering controls, and personal protective equipment, which are deemed necessary to ensure employee protection.
The CHP must include the following specific elements:
- Standard operating procedures (SOPs): Prudent operating procedures relevant to safety and health must be established for each activity involving the use of hazardous chemicals.
- Implementation of exposure control measures: Criteria must be determined, which would invoke the implementation of specific safety control measures. Such criteria should rely upon the inherent dangers associated with the chemicals involved in the process. Many of these chemicals are toxic, flammable, explosive, reactive, and corrosive. Control measures to be considered include engineering controls, the use of personal protective equipment, hygiene practices, and administrative controls.
- Proper functioning of lab hoods and other protective equipment: The employer must take measures to ensure the adequate performance of exhaust hoods and other safety equipment, including eyewash fountains and emergency showers.
- Information and training: Laboratory workers must be provided with appropriate information and training to become knowledgeable about the hazards present in their laboratories.
- Laboratory activities requiring prior approval: Identification must be made of those procedures, activities, or operations that the employer believes to be sufficiently hazardous to warrant approval before work begins (e.g., a potentially explosive chemical).
- Medical consultation and examinations: Under certain circumstances, employees must be allowed to receive appropriate medical consultations and medical examinations relevant to their exposure to hazardous chemicals.
- Designation of responsible personnel: The employer must designate personnel responsible for the implementation of the CHP, including the selection of a chemical hygiene officer and, if appropriate, a chemical hygiene committee.
- Special precautions for particularly hazardous substances: Additional employee protection is required whenever there is exposure to particularly hazardous materials (e.g., select carcinogens, reproductive toxins, and substances with a high degree of acute toxicity). Consideration should be given to the establishment of a designated area, use of exhaust hoods or glove boxes, use of respirators and protective apparel, personal hygiene practices, the safe removal of contaminated waste, and decontamination procedures.
The CHP must be readily available to employees, employee representatives, and, upon request, to the assistant secretary of labor for OSHA or designee. The employer must review and evaluate the effectiveness of the CHP at least annually and update it as necessary.
Information and training
Information and training are essential tools for informing workers and managers about workplace hazards and controls so they can work more safely and be more productive. Such information and training must be provided at the time of the employees’ initial assignment and before assignments involving new hazardous chemicals or new exposure situations. Appropriate training will provide employees with the information they need before exposure occurs and help to prevent the occurrence of adverse safety and health effects. It will also give the workers the precautions necessary to protect themselves, including emergency procedures.
Training need not be conducted on each specific chemical found in the workplace, but may be done by categories or groups of hazard (e.g., carcinogens, sensitizers, acutely toxic agents) that are or may be encountered by an employee during his/her duties. Chemical-specific information must always be available through labels and safety data sheets. Follow-up refresher information and training should be provided.
Information that is to be to be communicated and made available to the employees include the following:
- The contents of this standard and its appendices
- The CHP and safety data sheets (SDS)
- Permissible exposure limits for OSHA regulated substances used in the work area or recommended exposure limits for other hazardous chemicals in the absence of an OSHA standard
- Signs and symptoms associated with exposures to hazardous chemicals used in the laboratory
- Reference materials (e.g., SDSs) which detail the hazards, safe handling, storage, and disposal of hazardous chemicals
Medical consultation and examinations
The employer must provide all employees who work with hazardous chemicals the opportunity to receive appropriate medical attention. Whenever an employee exhibits signs or symptoms associated with exposure to a hazardous chemical, the employee must undergo a medical examination. The employer must also provide employees with an opportunity to receive a medical consultation whenever an event takes place in the work area, such as a spill, leak, explosion, or other occurrence resulting in the likelihood of significant exposure to a hazardous chemical. The medical consultation is provided to determine the need for a medical examination. The employee must be allowed to receive any examinations recommended by the physician.
All medical examinations and consultations must be performed by or under the direct supervision of a licensed physician and provided at a reasonable time and place, without cost or loss of pay to the employee.
The employer must provide the physician the name of the hazardous chemical(s) to which the worker has been exposed and a description of the conditions under which the exposure occurred, including employee exposure monitoring results, if available. Exposure data inform physicians of the extent of occupational exposures. The physician must also be made aware of the signs and symptoms of exposure that the employee was experiencing.
Hazard identification
To ensure chemical safety in the laboratory, information about the identities and hazards of the chemicals must be available and understandable to workers. The employer must ensure that labels on incoming containers of hazardous chemicals are not removed or defaced. SDSs accompany incoming hazardous chemicals must be retained and made available to laboratory employees. An SDS contains precautions for handling and using harmful substances and includes information such as health hazards, fire and explosion hazards, physical characteristics, hazardous ingredients, personal protective equipment, and spill procedures. Furthermore, SDSs that accompany these shipments must be maintained and made accessible to laboratory personnel.
The following provisions apply to laboratory-generated chemical substances:
- The chemical is produced exclusively for the laboratory's use: If the composition of the chemical is known, the employer must determine if it is a hazardous chemical in accordance with the Hazard Communication Standard, 29 CFR 1910.1200. If the material is determined to be hazardous, appropriate training is required.
- The chemical produced is a byproduct: If the chemical composition is unknown, the substance must be considered hazardous and handled according to the CHP, which provides for appropriate employee protection.
- The chemical is produced and shipped to another user outside of the laboratory: The employer is considered to have become a manufacturer and therefore is subject to all relevant provisions of the Hazard Communication Standard, including requirements for the creation of SDSs and labeling.
Record keeping
The employer must establish and maintain for each employee an accurate record of any measurements taken to monitor employee exposure and any medical consultation and examinations, including tests or written opinions required by this standard. The employer must assure that such records are kept, transferred, and made available per 29 CFR 1910.1020.
Accurate records of work-related injuries, illnesses, and fatalities must be established and maintained following the requirements of 29 CFR 1904.
References:
Code of Federal Regulations, 29 CFR 1910.1450. Govt. Printing Office. Washington, DC 20402 [latest edition].
OSHA. 1990 – Preamble/Final Rule. Occupational Exposures to Hazardous Chemicals in Laboratories; Final Rule. Federal Register 55:3310-3326 (January 31).
No comments:
Post a Comment