Best Management Practice : Cooling Tower Management
Overview
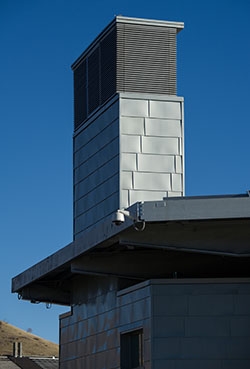
- Evaporation: This is the primary function of the
tower and is the method that transfers heat from the cooling tower
system to the environment. The quantity of evaporation is not a subject
for water efficiency efforts (although improving the energy efficiency
of the systems you are cooling will reduce the evaporative load on your
tower).
- Drift: A small quantity of water may be carried
from the tower as mist or small droplets. Drift loss is small compared
to evaporation and blowdown, and is controlled with baffles and drift
eliminators.
- Blowdown or bleed-off: When water evaporates from
the tower, dissolved solids (such as calcium, magnesium, chloride, and
silica) are left behind. As more water evaporates, the concentration of
dissolved solids increases. If the concentration gets too high, the
solids can cause scale to form within the system or the dissolved solids
can lead to corrosion problems. The concentration of dissolved solids
is controlled by blowdown. Carefully monitoring and controlling the
quantity of blowdown provides the most significant opportunity to
conserve water in cooling tower operations.
- Basin leaks or overflows: Properly operated towers should not have leaks or overflows. Check float control equipment to ensure the basin level is being maintained properly and check system valves to make sure there are no unaccounted for losses.
Make-up = Evaporation + Blowdown + Drift
A key parameter used to evaluate cooling tower operation is "cycles of concentration" (sometimes referred to as cycles or concentration ratio). This is calculated as the ratio of the concentration of dissolved solids (or conductivity) in the blowdown water compared to the make-up water. Since dissolved solids enter the system in the make-up water and exit the system in the blowdown water, the cycles of concentration are also approximately equal to the ratio of volume of make-up to blowdown water.
From a water efficiency standpoint, you want to maximize cycles of concentration, which will minimize blowdown water quantity and reduce make-up water demand. However, this can only be done within the constraints of your make-up water and cooling tower water chemistry. Dissolved solids increase as cycles of concentration increase, which can cause scale and corrosion problems unless carefully controlled.
In addition to carefully controlling blowdown, other water efficiency opportunities arise from using alternate sources of make-up water. Water from other equipment within a facility can sometimes be recycled and reused for cooling tower make-up with little or no pre-treatment, including the following.
- Air handler condensate (water that collects when warm, moist air
passes over the cooling coils in air handler units). This reuse is
particularly appropriate because the condensate has a low mineral
content, and typically is generated in greatest quantities when cooling
tower loads are the highest.
- Water used in a once through cooling system.
- Pretreated effluent from other processes, provided that any chemicals used are compatible with the cooling tower system.
- High-quality wastewater effluent or recycled water (where available).
Operation and Maintenance
To maintain water efficiency in operations and maintenance, Federal agencies should:-
Calculate and understand your "cycles of concentration." Check the
ratio of conductivity of blowdown and make-up water. Work with your
cooling tower water treatment specialist to maximize the cycles of
concentration. Many systems operate at two to four cycles of
concentration, while six cycles or more may be possible. Increasing
cycles from three to six reduces cooling tower make-up water by 20% and
cooling tower blowdown by 50%
-
The actual number of cycles you can carry depend on your make-up
water quality and cooling tower water treatment regimen. Depending on
your make-up water, treatment programs may include corrosion and scaling
inhibitors along with biological fouling inhibitors
-
Install a conductivity controller to automatically control blowdown.
Working with your water treatment specialist, determine the maximum
cycles of concentration you can safely achieve and the resulting
conductivity (typically measured as microSiemens per centimeter, uS/cm).
A conductivity controller can continuously measure the conductivity of
the cooling tower water and discharge water only when the conductivity
set point is exceeded
-
Install flow meters on make-up and blowdown lines. Check the ratio of
make-up flow to blowdown flow. Then check the ratio of conductivity of
blowdown water and the make-up water (you can use a handheld
conductivity meter if your tower is not equipped with permanent meters).
These ratios should match your target cycles of concentration. If both
ratios are not about the same, check the tower for leaks or other
unauthorized draw-off. If you are not maintaining target cycles of
concentration, check system components including conductivity
controller, make-up water fill valve, and blowdown valve
-
Read conductivity and flow meters regularly to quickly identify
problems. Keep a log of make-up and blowdown quantities, conductivity,
and cycles of concentration. Monitor trends to spot deterioration in
performance
-
Consider using acid treatment such as sulfuric, hydrochloric, or
ascorbic acid where appropriate. When added to recirculating water, acid
can improve the efficiency of a cooling system by controlling the scale
buildup potential from mineral deposits. Acid treatment lowers the pH
of the water and is effective in converting a portion of the alkalinity
(bicarbonate and carbonate), a primary constituent of scale formation,
into more readily soluble forms. Make sure workers are fully trained in
the proper handling of acids. Also note that acid overdoses can severely
damage a cooling system. The use of a timer or continuous pH monitoring
via instrumentation should be employed. Additionally, it is important
to add acid at a point where the flow of water promotes rapid mixing and
distribution. Be aware that you may have to add a corrosion inhibitor
when lowering pH
-
Select your water treatment vendor with care. Tell vendors that water
efficiency is a high priority and ask them to estimate the quantities
and costs of treatment chemicals, volumes of blowdown water, and the
expected cycles of concentration ratio. Keep in mind that some vendors
may be reluctant to improve water efficiency because it means the
facility will purchase fewer chemicals. In some cases, saving on
chemicals can outweigh the savings on water costs. Vendors should be
selected based on "cost to treat 1,000 gallons make-up water" and
highest "recommended system water cycle of concentration." Treatment
programs should include routine checks of cooling system chemistry
-
Consider measuring the amount of water lost to evaporation. Some
water utilities provide a credit to the sewer charges for evaporative
losses, measured as the difference between metered make-up water minus
metered blowdown water
-
Consider a comprehensive air handler coil maintenance program. As
coils become dirty or fouled, there is increased load on the chilled
water system to maintain conditioned air set point temperatures.
Increased load on the chilled water system not only has an associated
increase in electrical consumption, it also increases the load on the
evaporative cooling process, which uses more water.
Retrofit Options
The following retrofit options help Federal agencies maintain water efficiency across facilities:-
Install a sidestream filtration system composed of a rapid sand
filter or high-efficiency cartridge filter to cleanse the water. These
systems draw water from the sump, filter out sediments, and return the
filtered water to the tower. This enables the system to operate more
efficiently with less water and chemicals. Sidestream filtration is
particularly helpful if your system is subject to dusty atmospheric
conditions. Sidestream filtration can turn a troublesome system into a
more trouble-free system
-
Install a make-up water or sidestream softening system when hardness
(calcium and magnesium) is the limiting factor on cycles of
concentration. Water softening removes hardness using an ion exchange
resin and can allow you to operate at higher cycles of concentration
-
Install covers to block sunlight penetration. Reducing the amount of
sunlight on tower surfaces can significantly reduce biological growth
such as algae
-
Consider alternative water treatment options, such as ozonation or
ionization, to reduce water and chemical usage. Be careful to consider
the life cycle cost impact of such systems
-
Install automated chemical feed systems on large cooling tower
systems (over 100 tons). The automated feed system should control
blowdown/bleed-off by conductivity and then add chemicals based on
make-up water flow. These systems minimize water and chemical use while
optimizing control against scale, corrosion, and biological growth.
Replacement Options
The following replacement options help Federal agencies maintain water efficiency across facilities:-
Get expert advice to help determine if a cooling tower replacement is
appropriate. New cooling tower designs and improved materials can
significantly reduce water and energy requirements for cooling. However,
since replacing a cooling tower involves significant capital costs, you
should investigate every retrofit, operations, and maintenance option
available and compare costs and benefits to a new tower
-
For specifics on this technology, consult with experts in the field.
Your first resource should be local or headquarters engineers, but do
not overlook input from experienced contractors or other Government
agencies.
No comments:
Post a Comment