8 Safety Strategies to Maintain a Secure Workplace in the Utility Industry
Wastewater, water, electric, and natural gas utilities expose your work-alone employees to a lot of risks and hazards every day. Electrical engineers and maintenance personnel usually work alone for extended periods of time on outdoor pumps, treatment plants, and high-voltage substations, which can be dangerous. Employees who work with toxic gases, chemicals, and other machinery are also exposed to dangers on a daily basis.
Workers in electric, natural gas, water, sewer, and other utilities share numerous safety concerns. Here are eight of them.
1. Electrical Safety
Most workplace incidents have occurred due to negligence in electrical safety, according to research done by the Electrical Safety Foundation International. There were hundreds of fatal electrical wiring accidents noted and thousands of injuries due to electrical hazards that were reported by the National Safety Council in the United States. The figure clearly states how important it is to take precautions and avoid common electrical mistakes that result in electrical accidents. It is not only the responsibility of the employer to provide a safe environment for work but also the responsibility of the employees to make the workplace safe. However, training should be conducted to teach employees to use electrical equipment properly to avoid workplace fatalities.
2. Transmission Lines
Utility-line work ranks in the top 10 most dangerous jobs in the country, as around 30 to 50 workers per 100,000 are killed annually, according to a survey by Transmission and Distribution World. A lot of them also tend to suffer from mechanical trauma, electrical burns, and loss of limbs. When it comes to working on high-voltage overhead lines, there are a few safety measures to follow:
- Before getting work started, the overhead lines must be de-energized and grounded.
- While de-energizing lines, special arrangements should be made with the person or organization that handles electric circuits that de-energize lines.
- Protective measures such as insulating, guarding, or isolating should be taken to prevent employees from coming in direct or indirect contact with conductive materials.
3. Slips, Trips, and Falls
Sometimes, a hazardous situation can cause slips, trips, and falls. The U.S. Department of Labor’s Bureau of Labor Statistics reports that 800 nonfatal cases occurred in 2014 alone. Prevention is better than a cure. Slips and trips both occur due to an unexpected change in contact between the feet and surface while walking. With proper preventive measures and safety training, such hazards can be avoided.
4. Cold Stress
Prolonged exposure to freezing temperatures can lead to some serious health issues like hypothermia, frostbite, and trench foot. Cold water immersion can be a cause of death in extreme cases. Moreover, according to the Centers for Disease Control and Prevention, workers who are exposed to extremely cold weather are at risk of cold stress, which can lead to chilblains, trench foot, frostbite, and hypothermia. One way to avoid this is by limiting exposure to cold environments. Workers can schedule their work in the middle of the day or plan shorter shifts.
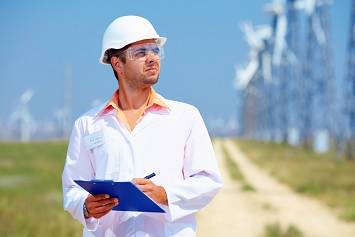
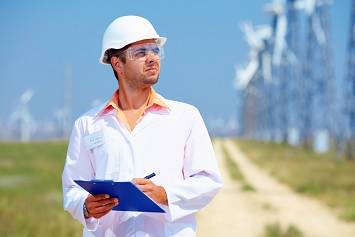
5. Heat Stress
Workers who constantly work in extremely hot environments are at risk of being exposed to heat stress. Constant exposure to extreme heat can lead to heat exhaustion, heat rashes, heat cramps, and heat strokes. Hot work environments increase the chances of injury and burns for your workers due to dizziness, fogged-up safety glasses, and sweaty palms.
Firefighters, farmers, boiler room workers, miners, factory workers, and construction site workers are at the most risk of heat stress. Workers aged 65 and over or with high blood pressure should avoid working in such environments, as it increases the risk of heat stress. Proper training on how to control heat stress in workplace-specific conditions will help prevent injuries and illnesses.
6. Physical Strain and Overexertion
Are your employees used to working long hours in a fast-paced environment? If yes, this is a problem, as these kinds of work environments lead to overexertion and fatigue, which can lead to accidents and injuries. Allowing your employees to take regular short breaks and change tasks will keep them alert and minimize their chances of injuries.
7. Biological and Chemical Hazards
Hepatitis is the most serious viral risk that your workers are exposed to when working with chemical hazards, and the most serious bacterial risk is tetanus, which occurs via hand-to-mouth contact.
Constantly being exposed to sewage can lead to infection of the eyes or skin, asthma, and hepatitis. Take all necessary safety measures when working in environments that have biological or chemical hazards.
8. Emergency Response
Do you have an emergency response protocol in place? If yes, is it up to date?
If an unexpected situation arises, you should be confident that all the processes and policies that you have in place will cover your lone workers and keep them safe. Your team should be prepared to tackle all unexpected situations as they arise.
The program you have in place should be clear, measured, and well-communicated so that any potential for health issues or injuries can be quickly pinpointed to the exact location where it might arise.
Do you have these eight safety issues covered? If not, don’t delay—find out how to improve your safety monitoring program today!
No comments:
Post a Comment