11 tips for effective workplace housekeeping
Every worker plays a part
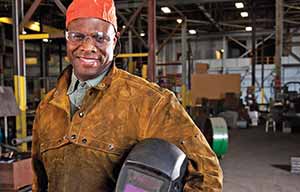
Key points
To some people, the word “housekeeping” calls to mind cleaning floors and surfaces, removing dust, and organizing clutter.- Housekeeping can help prevent injuries and improve productivity.
- Every worker should play a role in housekeeping, even if that means keeping his or her own workspace clean.
- Housekeeping should be an ongoing process, not a one-time practice.
But in a work setting, it means much more. Housekeeping is crucial to safe workplaces. It can help prevent injuries and improve productivity and morale, as well as make a good first impression on visitors, according to Cari Gray, safety consultant for the Ohio Bureau of Workers’ Compensation. It also can help an employer avoid potential fines for non-compliance.
The practice extends from traditional offices to industrial workplaces, including factories, warehouses and manufacturing plants that present special challenges such as hazardous materials, combustible dust and other flammables. Experts agree that all workplace safety programs should incorporate housekeeping, and every worker should play a part. In addition, housekeeping should have management’s commitment so workers realize its importance. Here are 11 tips for effective workplace housekeeping.
1

Slips, trips and falls were the second leading cause of nonfatal occupational injuries or illnesses involving days away from work in 2013, according to data from the Bureau of Labor Statistics.
OSHA’s Walking-Working Surfaces Standard (1910.22(a)) states that all workplaces should be “kept clean and orderly and in a sanitary condition.” The rule includes passageways, storerooms and service rooms. Floors should be clean and dry. Drainage should be present where “wet processes are used.”
Employers should select adequate flooring (e.g., cement, ceramic tile or another material), as different types of flooring hold up better under certain conditions, said Fred Norton, technical director of ergonomics and manufacturing technology for Risk Control Services, Liberty Mutual Insurance in Walnut Creek, CA. Then, develop and implement housekeeping procedures using appropriate cleaners.
“Things like oils and grease – if you don’t use the right kind of cleaning protocols, you’ll just spread slipperiness around rather than getting it up and off the floor,” Norton said.
To help prevent slip, trip and fall incidents, the Canadian Center for Occupational Health and Safety recommends the following:
- Report and clean up spills and leaks.
- Keep aisles and exits clear of items.
- Consider installing mirrors and warning signs to help with blind spots.
- Replace worn, ripped or damage flooring.
- Consider installing anti-slip flooring in areas that can’t always be cleaned.
- Use drip pans and guards.
Gray added that employers should audit for trip hazards, and encourage workers to focus on the task at hand.
2
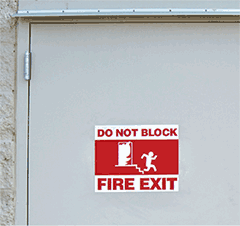
Employees are responsible for keeping unnecessary combustible materials from accumulating in the work area. Combustible waste should be “stored in covered metal receptacles and disposed of daily,” according to OSHA’s Hazardous Materials Standard (1910.106).
The National Safety Council “Supervisors’ Safety Manual” includes these precautionary measures for fire safety:
- Keep combustible materials in the work area only in amounts needed for the job. When they are unneeded, move them to an assigned safe storage area.
- Store quick-burning, flammable materials in designated locations away from ignition sources.
- Avoid contaminating clothes with flammable liquids. Change clothes if contamination occurs.
- Keep passageways and fire doors free of obstructions. Stairwell doors should be kept closed. Do not store items in stairwells.
- Keep materials at least 18 inches away from automatic sprinklers, fire extinguishers and sprinkler controls. The 18-inch distance is required, but 24 to 36 inches is recommended. Clearance of 3 feet is required between piled material and the ceiling. If stock is piled more than 15 feet high, clearance should be doubled. Check applicable codes, including Life Safety Code, ANSI/NFPA 101-2009.
- Hazards in electrical areas should be reported, and work orders should be issued to fix them.

Dust accumulation of more than 1/32 of an inch – or 0.8 millimeters – covering at least 5 percent of a room’s surface poses a significant explosion hazard, according to the Quincy, MA-based National Fire Protection Association. This dust accumulation is about as thick as a dime or paper clip. An industrial hygienist should test the workplace for exposures if air quality and dust are concerns, Gray said.
NFPA 654 – a standard on preventing fire and dust explosions
– addresses identifying hazard areas, controlling dust and
housekeeping. The standard states that vacuuming is the “preferred”
method of cleaning. Sweeping and water wash-down are other options.
“Blow-downs” using compressed air or steam is allowed for inaccessible
or unsafe surfaces.
Industrial vacuums can clean walls, ceilings, machinery and other places, CCOHS notes.“You want to use wet methods or have high-efficiency vacuum systems,” said Steve Ahrenholz, senior industrial hygienist at NIOSH’s Division of Surveillance, Hazard Evaluations and Field Studies. “You don’t want to use just a shop vac or dry-sweep it – definitely not using compressed air to blow it. [Then] you’re just re-suspending the dust and distributing it all over.”
Dust also can affect equipment’s length of life and quality of products, Ahrenholz added.
4

Work-area mats – which can be cloth or sticky-topped – should be kept clean and maintained. This helps prevent the spread of hazardous materials to other work areas or home, Gray said. Check all mats to ensure they are not tripping hazards.
Additionally, separate cleaning protocols may be needed for different areas to prevent cross-contamination, Norton notes. Avoid using the same mop to clean both an oily spill and in another area, for example.
If the materials are toxic, industrial hygiene testing, uniforms and showering facilities might be needed, Gray said. Employees who work with toxic materials should not wear their work clothes home, Ahrenholz added.
5

Gray noted that protections such as a toe board, toe rail or net can help prevent objects from falling and hitting workers or equipment.
Other tips include stacking boxes and materials straight up and down to keep them from falling, said Paul Errico, a Fairfield, CT-based safety consultant. Place heavy objects on lower shelves, and keep equipment away from the edges of desks and tables. Also, refrain from stacking objects in areas where workers walk, including aisles.
Keep layout in mind so workers are not exposed to hazards as they walk through areas, Norton added.
6

Clear clutter
A cluttered workplace can lead to ergonomics issues and possible injuries because workers have less space to move, Gray said.
“When an area is cluttered, you’re going to likely have a cut or laceration injury,” she said. “You’re not going to have as much room to set up your workstation like you should and move around. You’re going to be twisting your body rather than moving your whole body.”
The Ohio Bureau of Workers’ Compensation recommends that workers return tools and other materials to storage after using them, and dispose of materials that are no longer needed.
Keep aisles, stairways, emergency exits, electrical panels and doors clear of clutter, and purge untidy areas. Empty trash receptacles before they overflow.
7

According to OSHA’s Materials Handling, Storage, Use and Disposal Standard (1926.250), storage areas should not have an accumulation of materials that present hazards for tripping, fire, explosion or pests.
Some workers make the mistake of storing ladders or other items inside electrical closets where they can block an electrical panel, creating a fire hazard and violating OSHA regulations, Errico said.
“I found that in a couple places. That would surprise employers if they’re not looking for it,” Errico said. “It’s important that they stay on top of it; realize it’s not just the manufacturing floor, maintenance area, warehouse or main storage areas, but these little areas in buildings that create a problem with storage.”
Unused materials and equipment should be stored out of the way of workers. Avoid using workspaces for storage, according to CCOHS. And remember to put everything back in its proper place, Ohio BWC adds.
Ahrenholz recommends keeping a storage space nearby so workers are encouraged to use it.
“There’s a responsibility to keep your work area in order and return tools to where they belong,” he said. “The storage space, if readily useable, is designed in such a way where it can be used without stretching too far or lifting heavy loads. They’re more likely to use it than if they have to go quite a ways to place something. Or they’re going to keep something rather than go back because they have to take the extra time to get it.”
8

Errico has seen workers’ compensation cases stemming from employees who did not wear PPE when cleaning up spills or other material, such as broken glass or plywood, and then suffered cuts or splinters.
Wear basic PPE – such as closed-toe shoes and safety glasses – while performing housekeeping, Gray said. Determine what type of PPE to don based on the potential risks.
Regularly inspect, clean and fix tools, according to CCOHS. Remove any damaged tools from the work area.
9

All workers should participate in housekeeping, especially in terms of keeping their own work areas tidy, reporting safety hazards and cleaning up spills, if possible.
“Every worker does have a role in housekeeping,” Ahrenholz said. “If they see something is becoming a problem, they need to report it.”
Before the end of a shift, workers should inspect and clean their workspaces and remove unused materials. This dedication can reduce time spent cleaning later, experts say.
How much debris or contaminants the workplace releases can help determine the frequency of housekeeping. A company should have a mixture of deep cleaning and more frequent, lighter cleaning that involves sweeping and responding to spills, Norton said.
10

Experts agree that housekeeping policies should be put in writing. That way, Norton said, they are formal and defined. Written protocols could specify which cleaners, tools and methods should be used. “We found there are many gaps in the effectiveness of floor cleaning in the operations we’ve done research on,” Norton said. “It is an area that sometimes gets overlooked. That’s why we think it’s important for the written part of the protocols and defined training so people are aware of and follow the proper procedures.”
11

Housekeeping should be more than a one-time initiative – it should continue through monitoring and auditing. Keep records, maintain a regular walkthrough inspection schedule, report hazards and train employees to help sustain housekeeping. Set goals and expectations, and base auditing on those goals, Gray said.
“Housekeeping issues are very common. They can be easy to fix,” she said. “It’s going to take persistence and dedication.”
Great Information! Its looking Nice. Safety is most important. Useful for me to develop my knowledge. Thank you!
ReplyDeleteCorporate Training Chennai - Safety Training
Nebosh IGC in Chennai
Nebosh Course in Vizag
Nebosh Courses In Chennai
NEBOSH Course in Pondicherry
Industrial Safety Diploma Course In Chennai