Modern Research in Catalysis Vol.1 No.3(2012), Article ID:23592,9 pages DOI:10.4236/mrc.2012.13006
Evaluation Performance of Different Types Catalysts of an Industrial Secondary Reformer Reactor in the Ammonia Plants
Department of Chemical Engineering, Basra University, Basra, Iraq
Email: *chemicalengineer82@yahoo.com
Received September 3, 2012; revised October 5, 2012; accepted October 15, 2012
Keywords: Fertilizers; Autothermal Reformer; Steam Reforming; Catalysis; Hydrogen Production.
ABSTRACT
In
this paper, the effect of catalyst shape and characteristics has been
investigated where five types of a catalyst were examined under the same
operation conditions, where catalysts are similar in the chemical
properties (Ni/MgOAl2O3) but it's different in
their physical properties in the catalyst section of secondary reformer.
The secondary reformer involves continuation of the methane reforming
reaction that began in the primary reformer to produce Nitrogen and
Hydrogen in the ammonia plant. In order to evaluate performance of
various types of catalysts in the secondary reformer reactor,
mathematical model have been created. The mathematical model covers all
aspects of major chemical kinetics, heat and mass transfer phenomena in
the secondary reformer in the ammonia plant at steady state conditions.
It aims to optimize the best catalyst from five types of catalyst of the
secondary reformer reactor in the State Company of Fertilizers South
Region in the Basra/Iraq. The mathematical model allows calculating the
axial variations of compositions, temperature and pressure of the gases
inside two reactors in series by using the atomic molar balance and
adiabatic flame temperature in the combustion section while, in the
catalyst section, they are predicted by using a one-dimensional
heterogeneous catalytic reaction model. The analysis evaluation
performance of the catalyst (RKS-2-7H’) have good results than other the
catalyst types (RKS - 2, ICI 54 - 2, RKS-2-7H”, RKS-2-7H”’) in catalyst
zone of the secondary reformer.
1. Introduction
In
a traditional ammonia plant, the secondary reformer is rather used
downstream of the primary reformer in order to reform the unreacted
methane to produce Hydrogen and Nitrogen.The reactor consists of two sections, the combustion section is the empty space above the catalyst section is preferred to combust process gases with oxygen of the air to produce the Nitrogen while, the catalytic section is a fixed-bed reactor, in which the hydrocarbons are finally converted through heterogeneous catalytic reactions to produce the Hydrogen. It is provided with Ni/MgOAl2O3 as a catalyst, Finally, the Reformat Gases leaves the secondary reformer, as shown in the Figure 1.
1) Burner; 2) Combustion section; 3) Alumina bricks plate; 4) Alumina balls (dia. = 40 mm); 5) Catalyst section; 6) Alumina balls (dia. = 40 mm, 75 mm and 120 mm); 7) Cone.
The previous studies focuses on the secondary reformer in the ammonia plants or Autothermal reformer mainly Ali AL-Dhfeery and Ala’a Jassem [1], Akbar Zamaniyan
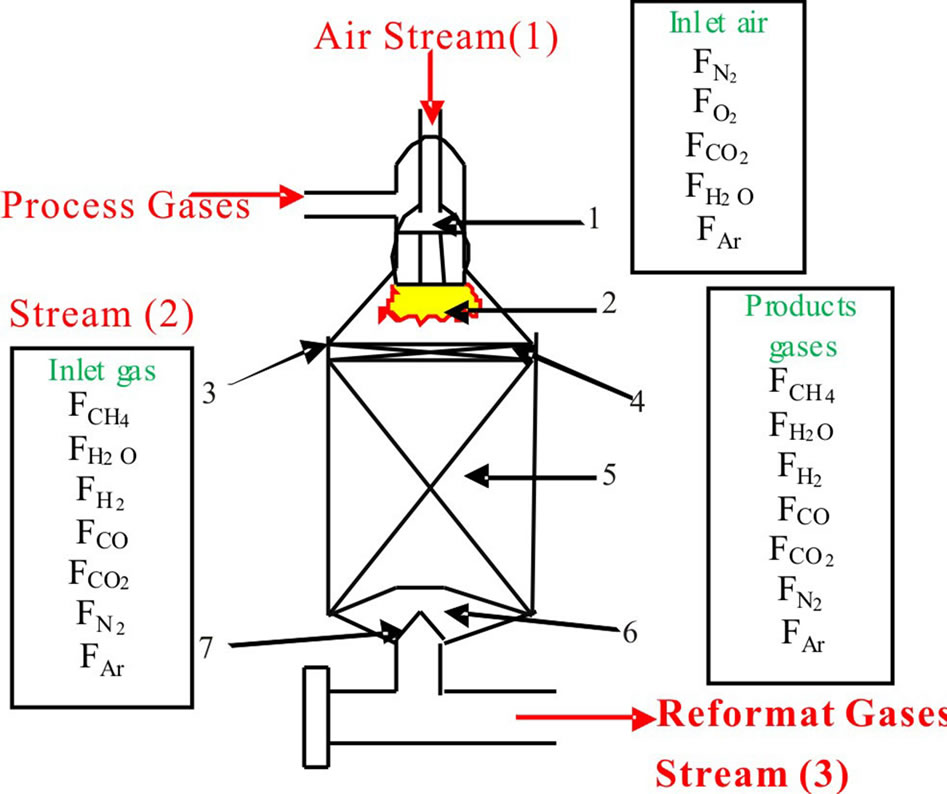
Figure 1. Schematic diagram of secondary reformer [1].
The results of mathematical model such as mole fraction, temperature profile and pressure drop of the combustion and catalyst zones of secondary reformer reactor in the State Company of Fertilizers South Region in the Basra/Iraq will be studied and compared relative to five different types of Ni-catalyst.
2. Experimental Section
The
type of catalyst is considered one of the most important factors in
industrial catalytic reactors which affect the conversion of reactants
and the yield of the products.
The catalyst of reformer generally
uses nickel catalysts due to high activity with high surface area to
accelerate the reforming reactions.
A Ni-catalyst support on a
magnesia-alumina spinel has used in the top of the catalyst bed in the
secondary reformer reactor because it is activity and stability at
high-temperature without breaking or shrinking where, the top of the
catalyst bed is exposed to gases with high temperature of 1100˚C -
1400˚C [9].A reforming catalyst, type RKS, is used for the steam reforming of natural gas. This catalyst is well suited for use in both, low temperatures in the primary reformer and at high temperatures in secondary and autothermal reformers for the production of hydrogen [10].
The nickel catalysts RKS-2 with one hole are packed with the volume of 26 m3, height of the catalyst bed 2.8 m with inside diameter of industrial secondary reformer reactor in ammonia unit in the State Company of Fertilizers South Region in the Basra/Iraq, is 3.45 m. The five various types of catalysts are used in a secondary reformer is summarized in Table 1.
3. Mathematical Model
In
this section, the evaluation of performance for five different types of
catalysts have been examined depending on the creating of a
mathematical model relative to the actual operation conditions in the
secondary reformer at Basrah Fertilizers Plant.
3.1. Modeling of Combustion Section
3.1.1. Chemical Reactions
The
hydrocarbon (CH4) and oxygen in the air are mixed and combusted in the
combustion section of secondary reformer reactor. Often the principle
“mixed is burnt” is valid, since the exothermic combustion reactions are
very fast.The homogenous reactions are take place in the combustion section. The combustion reactions are numerous complex radical reactions, but for modeling purposes, it is often enough to describe the reactions by an overall one molecular reaction. In the case of natural gas, the
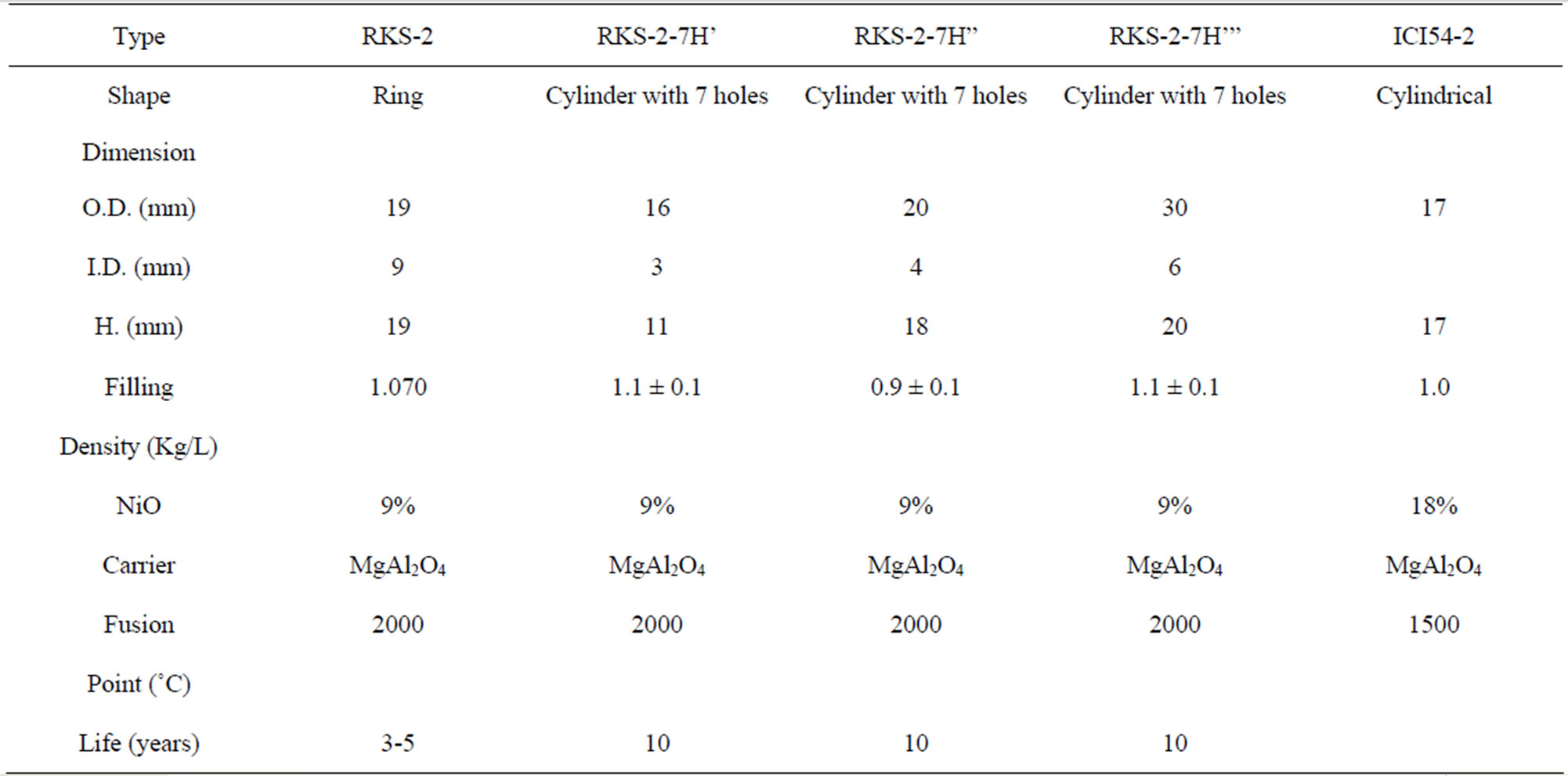
Table 1. Depicts types of catalysts using in secondary reformer [9-11].


3.1.2. Mass and Heat Balances
The
compositions and temperature of the gas in the combustion section is
investigated by using simple mathematical model. The atomic molar
balance and adiabatic flame temperature are used with assuming that the
mixing between process gases and air is instantaneous in combustion
section, and the conditions inside and outside of combustion section are
same.The atomic molar balance for each gas component in the combustion section can be derived as follows [1]:
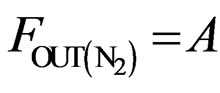
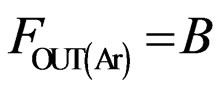
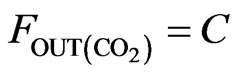
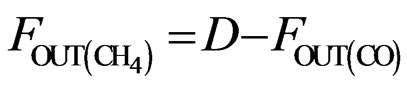



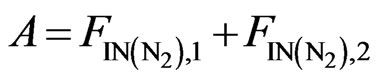
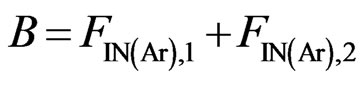

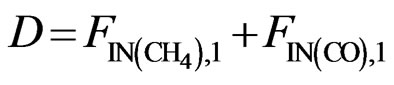


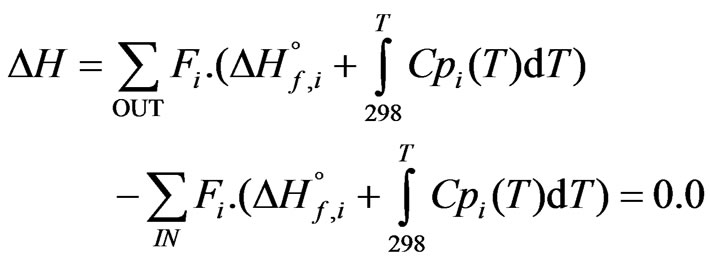
3.2. Modeling of Catalyst Section
3.2.1. Chemical Reactions
The
product gas from the combustion section is directed to the catalytic
section of the secondary reformer. The catalyst bed involves three
reversible reactions, which were thoroughly studied by Xu and Froment
(1989). The first reaction is known as a Steam Methane Reforming
reaction while the second and third reactions are called as Water Gas
Shift reaction and Carbon Dioxide Reforming reaction respectively.
Anyway, the following equations can be written as follows: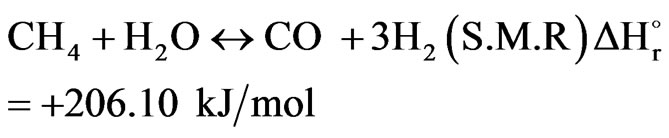
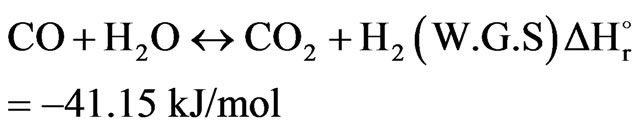

3.2.2. Kinetics of the Reforming Reactions
The
kinetics for the reforming reaction of methane on the Nickel catalyst
based on the Alumina is according to study of Xu and Froment given in
[1].
3.2.3. Effectiveness Factor Analysis
The
effectiveness factor is an important parameter to predict the
temperature and composition profiles for realizing the actual reaction
rate with pore diffusion in the heterogeneous reaction. The
effectiveness factor can be calculated by using the following equation
[13]: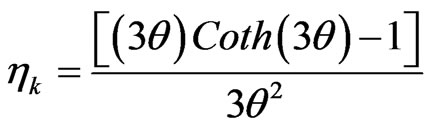
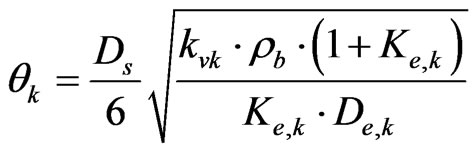
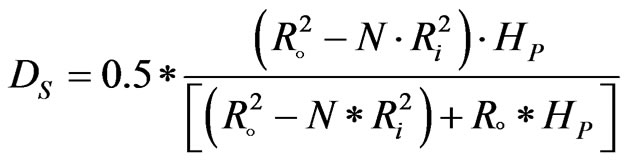
3.2.4. Mass, Heat and Momentum Balances
The
concentration and temperature gradient is assumed to occur only in the
axial direction while, the radial gradients temperature and composition
are ignored because the reactor operates under adiabatic conditions.
Through, the adiabatic one dimensional heterogeneous catalytic reaction
model can be applied in the catalyst section by the following equations
[8]:
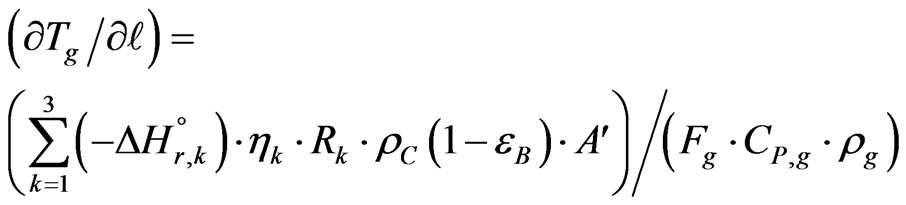
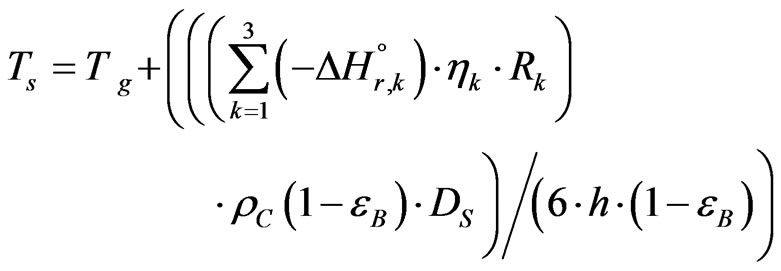
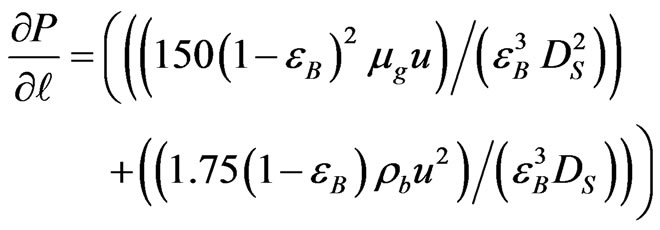
4. Results and Discussion
4.1. Combustion Section
The actual operating conditions such as feed concentration, temperature and pressure have tabulated in Table 2.
These data have used for modeling and evaluating the theoretical
performance of industrial secondary reformer reactor. In addition to,
there is no industrial data available in this section therefore they are
not comparable.
4.2. Catalyst Section
In
this section, the theoretical results predication from mathematical
model have compared with the industrial data which collected from the
manual and daily log sheet of Basra Fertilizer Plant where, the catalyst
characteristics have been calculated from mathematical model for five
different types catalysts as summarized in Table 3. The results depicted high accuracy between Simulation results and Plant Data [1].
4.2.1. Molar Flow Rates of Reactants and Products
In
this section, the influence of the different types of catalysts is
discussed with respect to the molar flow rates of reactants and products
in the catalyst zone of the secondary reformer at Basrah Fertilizers
Plant.The relation between molar flow rates of gases as a function of the axial coordinate of catalyst bed has been described in Equation (23).
Figures 2-7 depict the effect of molar flow rates of methane, steam, Hydrogen, Carbon monoxide, Carbon di-
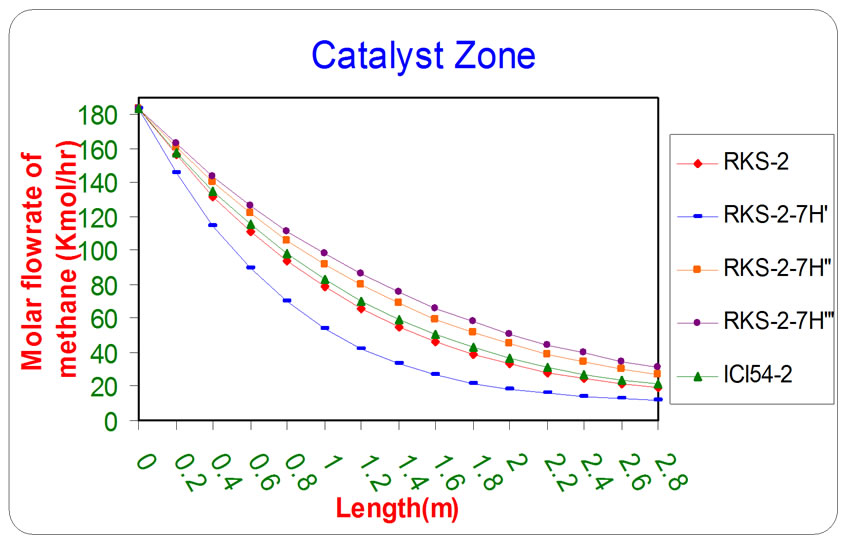
Figure 2.
The influence of the difference types of catalyst on the molar flow
rate of methane as a function of reactor length relative to inlet
operation conditions (T = 1369.644 K & P = 32 bar).
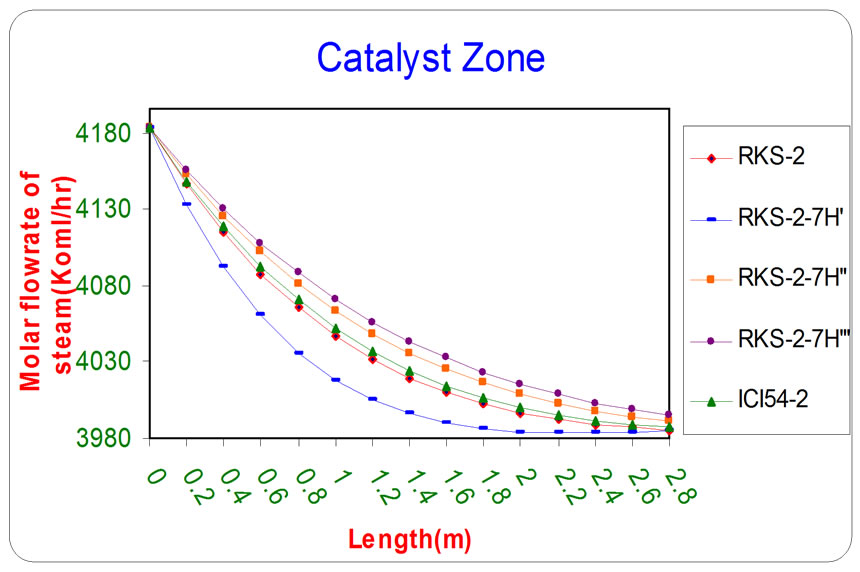
Figure 3.
The influence of the difference types of catalyst on the molar flow
rate of steam as a function of reactor length relative to inlet
operation conditions (T = 1369.644 K & P = 32 bar).
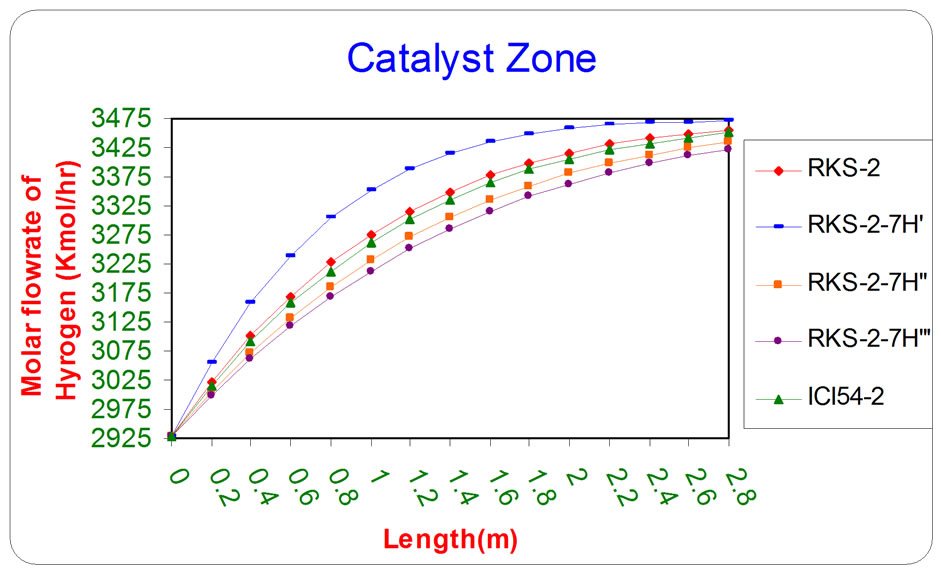
Figure 4.
The influence of the difference types of catalyst on the molar flow
rate of Hydrogen as a function of reactor length relative to inlet
operation conditions (T = 1369.644 K & P = 32 bar).
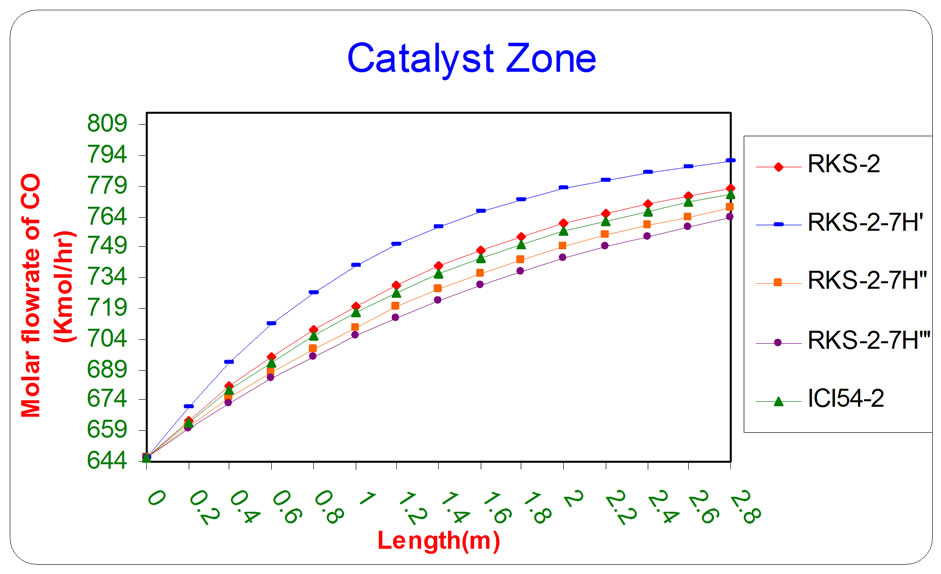
Figure 5.
The influence of the difference types of catalyst on the molar flow
rate of CO as a function of reactor length relative to inlet operation
conditions (T = 1369.644 K & P = 32 bar).
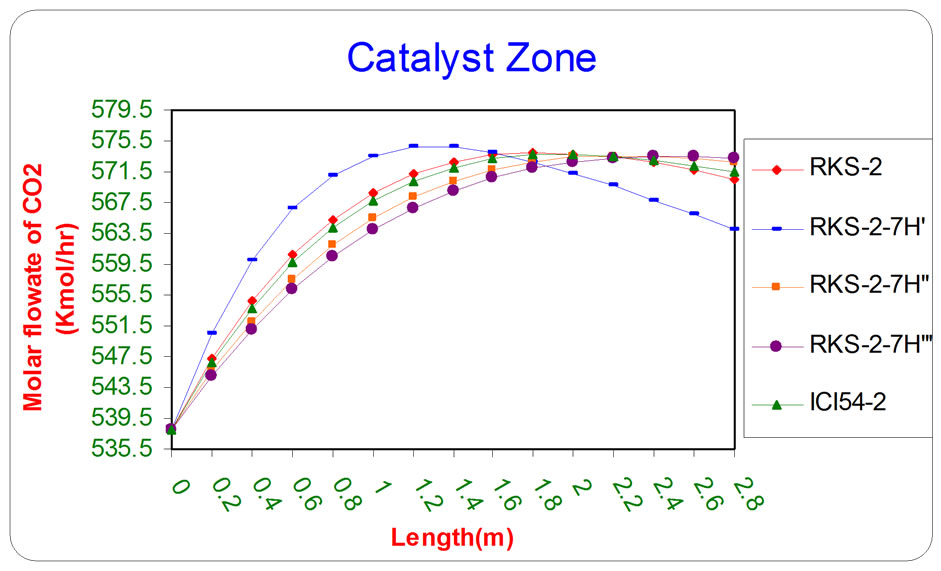
Figure 6. the influence of the difference types of catalyst on the molar flow rate of CO2 as a function of reactor length relative to inlet operation conditions (T = 1369.644 K & P = 32 bar).
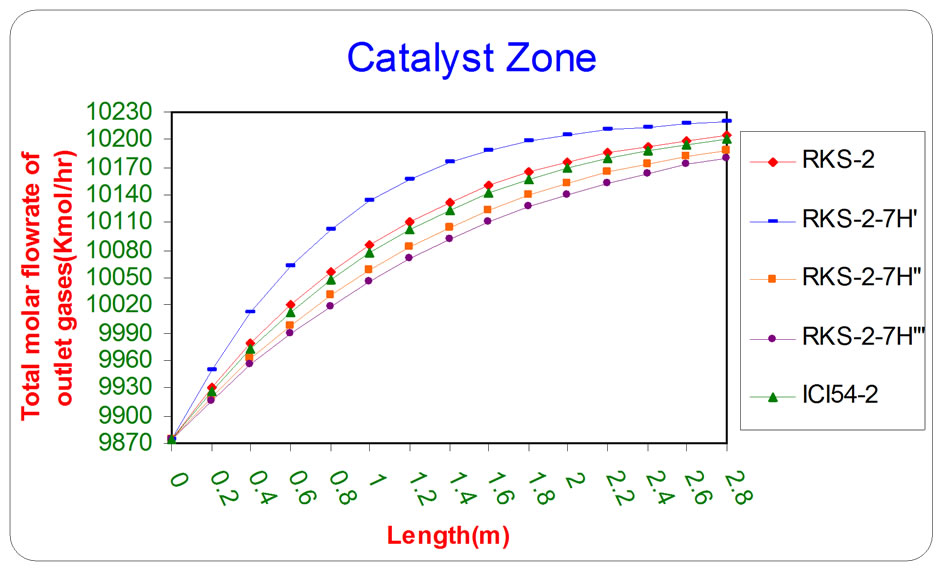
Figure 7.
the influence of the difference types of catalyst on the total molar
flow rate of outlet gases from catalyst section as a function of reactor
length relative to inlet operation conditions (T = 1369.644 K & P =
32 bar).
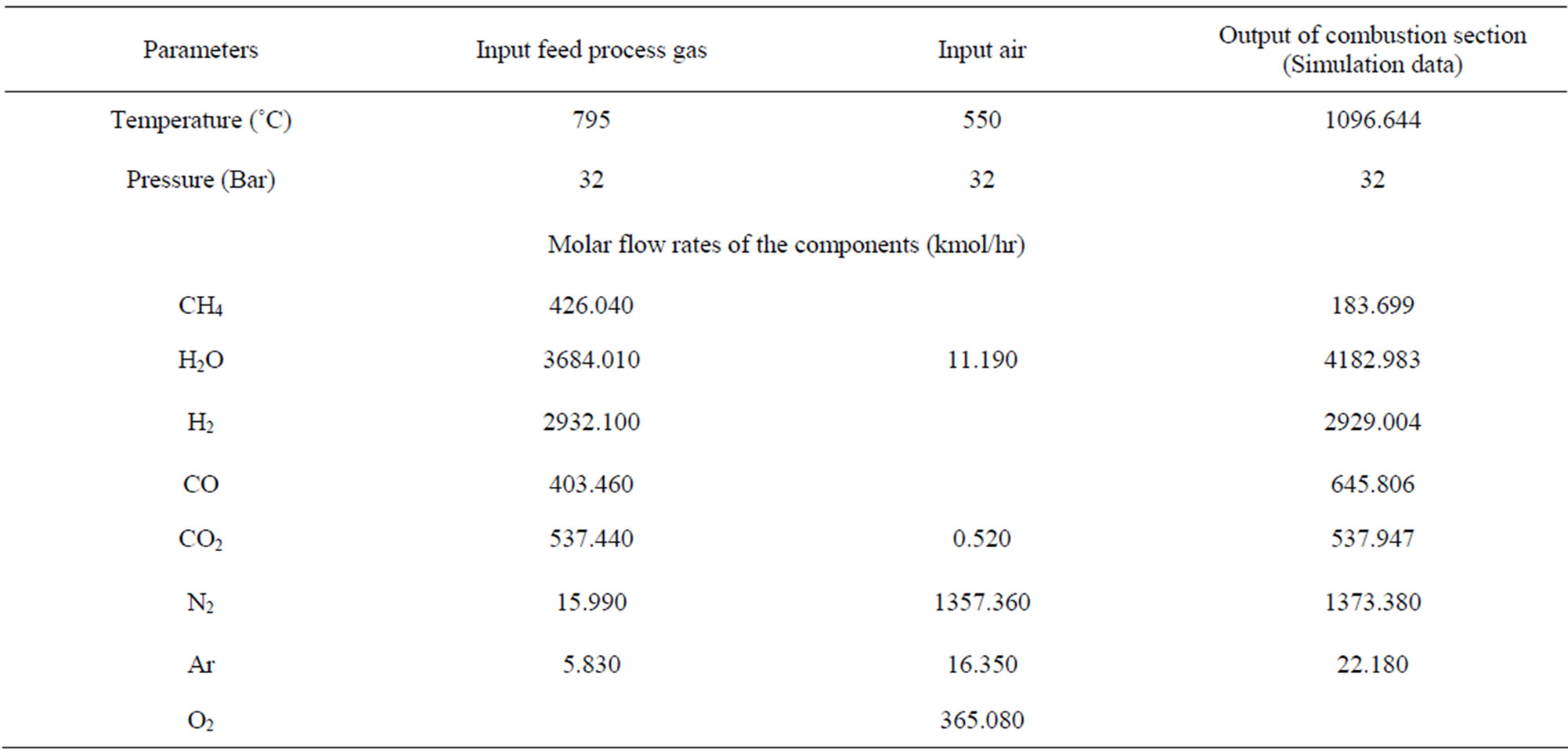
Table 2.
Depicts the actual operations conditions of industrial secondary
reformer in S.C.F.S.R. in Basra/Iraq with the simulation Data of the
combustion section [14].
All the previous figures depict the catalyst (RKS-2- 7H’) was the best one relative to any other types. This is due to it appears more methane and steam consumption with more Hydrogen and carbon monoxides production.
4.2.2. Temperature Calculation for Gases and Catalyst Surface
The
temperature is considered a very important factor due to the nature of
chemical reactions on the catalyst section. These reactions are extended
from endothermic to exothermic. The relation between the temperature of
gases and surface of catalyst as a function for axial coordinate of
catalyst bed has been described in Equations 24 and 25.Figures 8 and 9 depict that the catalyst (RKS - 2 - 7H’) was more active than the other catalyst types (RKS - 2, ICI 54 - 2, RKS - 2 - 7H” and RKS-2 - 7H”’) respectively relative to the reactions conditions because the temperatures of gases and catalyst surface are lower than the temperatures in the other types of catalysts due to endthermic reactions that means the rate of reactions on the catalyst surface (RKS-2-7H’) are faster than other types of catalysts.
4.2.3. Pressure Drop
The
pressure drop gives a good indication about catalyst performance inside
the reaction shell because with a long time of operation; the catalyst
may be thermal cracking due to high operation temperature so, the value
of pressure drop will increase.When the heat load per unit area is too high, smaller particles will be necessary in order to increase the surface area of the catalyst but, smaller particles will lead to increase the pressure drop. Therefore, selecting special
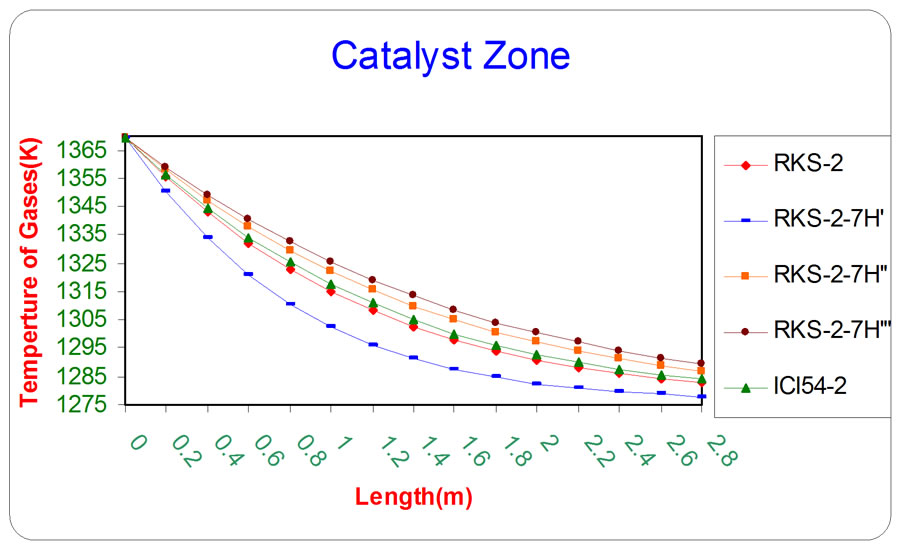
Figure 8.
The influence of the difference types of catalyst on the temperature of
gases as a function of reactor length relative to inlet operation
conditions (T = 1369.644 K & P = 32 bar).
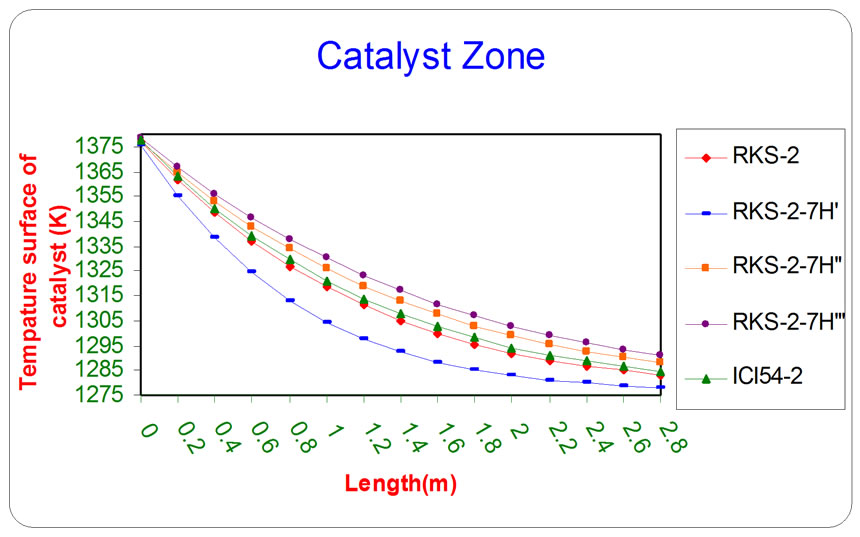
Figure 9.
The influence of the difference types of catalyst on the temperature of
catalyst surface as a function of reactor length relative to inlet
operation conditions (T = 1369.644 K & P = 32 bar).
The behavior of pressure drop has been described in Equation (26) which depicts a decrease along the axial distance from the top of the catalyst bed.
Figure 10 depicts the value of outlet pressure as a function of reactor length for five different types of catalysts.
5. Conclusions
Secondary
reformer for Hydrogen and Nitrogen production is mathematically
investigated by a series of simulation of operation conditions which
have collected from the documents of Basra Fertilizer Plant. Although,
the catalyst (RKS-2) has been using in the secondary reformer at Basrah
fertilizers plant but, the analysis evaluation performance of catalyst
(RKS-2-7H’) had good results than the other catalyst types (RKS-2, ICI
54-2, RKS-2-7H” and RKS-2-7H”’) for several reasons as follows:
5.1. Gases Molar Flow Rates, Temperature of Gases and Catalyst Surface
This
type of catalyst appears more methane and steam consumption with more
Hydrogen and carbon monoxides production. Also, the temperatures of
gases and catalyst surface are lower than the temperatures in the other
types of catalysts due to endothermic reactions that means the rate of
reactions on the catalyst surface (RKS- 2-7H’) are faster than other
types of catalysts.
5.2. The Shape of Pellet
The
shape of the catalyst pellet is considered a very important parameter.
Rings with several holes are suitable shape amongst secondary reforming
catalysts because it provides a higher surface area per unit volume i.e.
the specific surface area of the pellets (S) as summarized in Table 3.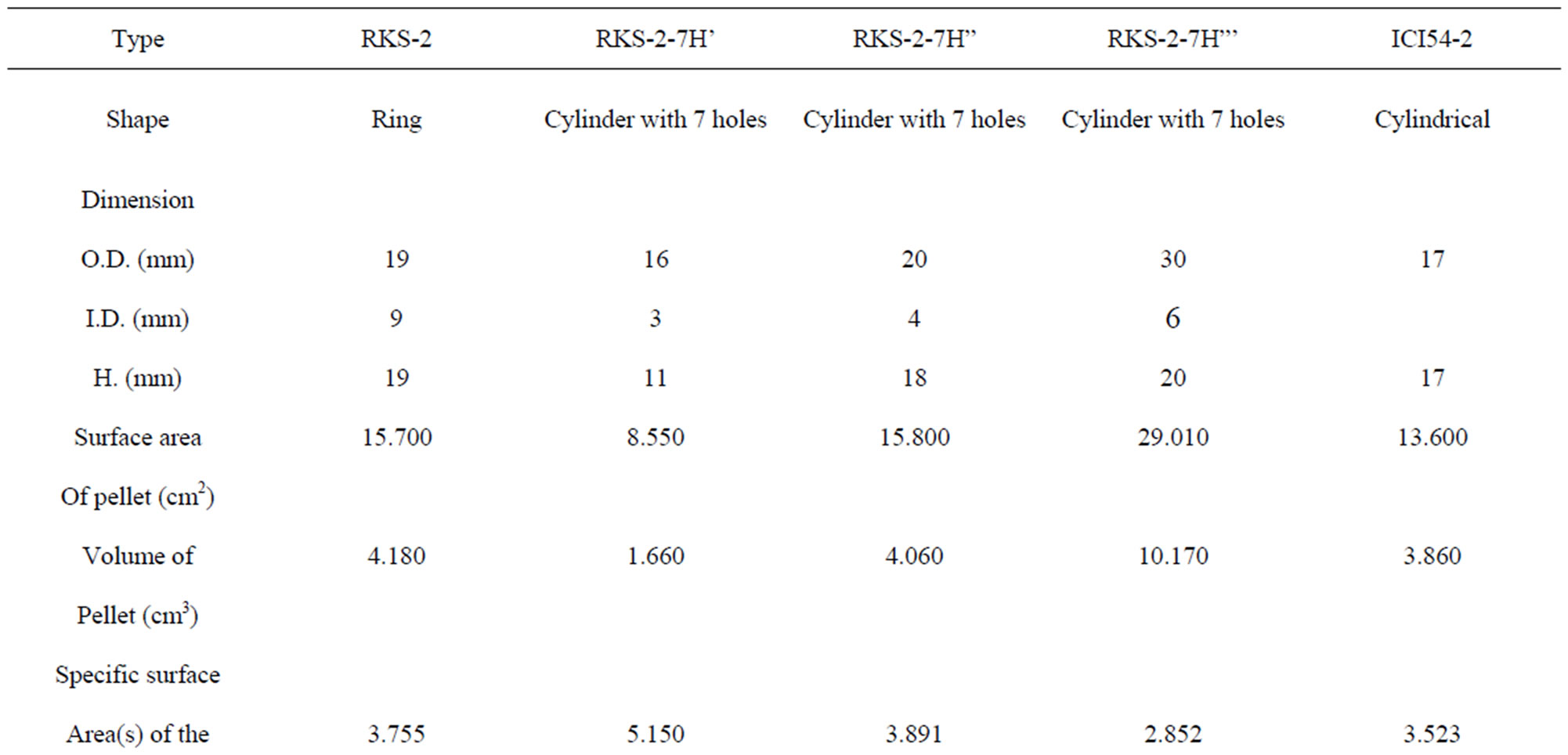

Table 3. Types of catalysts characteristics used in secondary reformer.
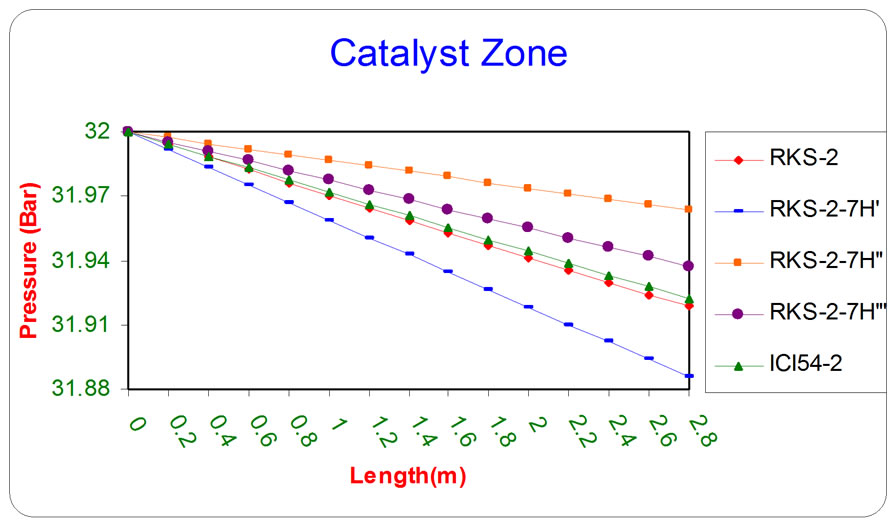
Figure 10.
the influence of the difference types of catalyst on the pressure as a
function of reactor length relative to inlet operation conditions (T =
1369.644 K & P = 32 bar).
5.3. The Total Surface Area of Catalyst Pellets in Catalyst Section
Using
the smallest of the pellet in the catalyst zone is necessary for
available high total surface area of catalyst pellets in catalyst
section as shown in Table 3.
5.4. Volume of Pellet
The
diffusion into the pellet is relatively slow, so that this condition
mean reaction occurs before the reactant has diffused far into the
pellet. Also, the effectiveness factor 
that means only the surface near from the outer surrounding of the pellet is effective, therefore, the diffusion and effectiveness factor gave a good indication about the shape of the catalyst that is used in the catalyst zone as a ring without central portion because the chemical reaction takes place at the outer surface [1], then the volume of RKS-2-7H’ pellet (Cylinder with 7 holes) has least volume of pellet because it has least dimensional and thin of walls than other pellets as shown in Table 3.
6. Acknowledgements
This
work has been co-supported by the State Company Fertilizers Plant South
Region to introduce industrial data for this investigation.
REFERENCES
- A. A. AL-Dhfeery and A. A. Jassem, “Modeling and Simulation of an Industrial Secondary Reformer Reactor in the Fertilizer Plants,” International Journal of Industrial Chemistry (IJIC), Vol. 3, No. 2012. doi:10.1186/2228-5547-3-14
- A. Zamaniyan, A. Behroozsarand and H. Ebrahimi, “Analysis of a Secondary Autothermal Reformer Using a Thermodynamic POX Model,” Journal of World Academy of Science, Engineering and Technology, Vol. 49, No. 25, 2009, pp. 247-251.
- J. A. C. Ruiz, F. B. Passos, J. M. C. Bueno, E. F. Souza-Aguiar, L. V. Mattos and F. B. Noronha, “Syngas Production by Autothermal Reforming of Methane on Supported Platinum Catalysts,” Applied Catalysis A: General, Vol. 334, No. 1-2, 2008, pp. 259-267. doi:10.1016/j.apcata.2007.10.011
- K. Khorsand and K. Deghan, “Modeling and Simulation of Reformer Autothermal Reactor in Ammonia Unit,” Journal of Petroleum and Coal, Vol. 49, No. 2, 2007, pp. 64-71.
- D. L. Hoang, S. H. Chan and O. L. Ding, “Hydrogen Production for Fuel Cells by Autothermal Reforming of Methane Over Sulfide Nickel Catalyst on a Gamma Alumina Support,” Journal of Power Sources, Vol. 159, No. 2, 2006, pp. 1248-1257. doi:10.1016/j.jpowsour.2005.11.094
- S. Vaccaro, G. Ferrazzano and P. Ciambelli, “Coupling of Catalytic Endothermic and Exothermic Reactions by CPR: Modeling and FEM simulation,” COMSOL Conference User, Millano, 2006.
- M. I. Shukri, A. R. Songip, A. Ahmad and N. S. Nasri, “Simulation Study of Methane Autothermal Reforming for Hydrogen Production,” Advanced in Fuel Cell Research, Fuel Cell Research Group, UTM, 2004, pp. 149- 158.
- Y. H. Yu, “Simulation of Secondary Reformer in Industrial Ammonia Plant,” Chemical Engineering Technology, Vol. 25, No. 3, 2002, pp. 307-314. doi:10.1002/1521-4125(200203)25:3<307::AID-CEAT307>3.0.CO;2-C
- G. W. Bridger and G. C. Chiclen, “Catalyst Handbook,” Wolrd Scientific, London, 1970.
- Mitsubishi Heavy Industries LTD MCEC, “Training Textbook,” Catalyst Manual of Ammonia Unit, Japan, 1977.
- H. Topsoe, “Topsoe Secondary Reforming Catalyst RKS- 2-7H,” www.topsoe.com
- R. M. Felder and R. W. Rousseau, “Elementary Principles of Chemical Processes,” 3rd Edition, John Wily & Sons Inc., Chichester, 2005.
- J. M. Smith, “Chemical Engineering Kinetics,” 2nd Edition, McGraw-Hill, New York, 1970.
- Mitsubishi Heavy Industries LTD MCEC, “Operation Manual,” Documents of State Company of Fertilizer Plant South Region, Japan, 1977.
Nomenclature
A’ = Cross section area (m2).CP = Specific heat capacity (kJ/kmol.K).
De,k = Effective diffusivity of i-component for reaction k is defined as

Di,mix = molecular diffusivity of i-component in the gas mixture
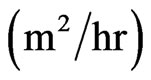
DKn,i = Kndsun diffusivity of i-component
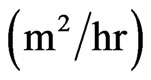
DS = Equivalent pellet diameter (m). This is defined as the diameter of a sphere with the same external surface area per unit volume of the catalyst pellet.
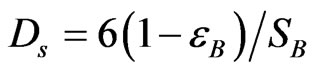
F = Molar flowrate (kmol/hr).
H = Heat transfer coefficient (kJ/m2. K.hr)
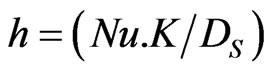
HP Height of pellet (m).
ΔH = Enthalpy change (kJ/kmol).
ΔHºf,i = Standard enthalpy of formation of i-component (kJ/mol).
ΔHor,k = Standard heat of reaction k (kJ/mol).
K = Thermal conductivity of gases (W/m.K).
Ke,k Equilibrium constant for reaction k (bar2) (except reaction number 2 dimensionless unit).
kυ,k The volumetric kinetic constant for reaction k (to convert unit of constant of reaction Rate) (m3/Kgcat.hr).
ℓ axial coordinates (m).
N Number of holes in the pellet of catalyst.
Nu Nessult number (dimensionless unit).
P Pressure of gases (Bar).
Q volumetric flowrate (m3/hr).
Pr Prandtl’s number (dimensionless unit).
Rk Rate of reaction for reaction k (kmol/Kgcat.hr).
R External radius of catalyst pellet of cylindrical shape (m).
Ri Inner radius of catalyst pellet of cylindrical shape (m).
S Specific surface area of the pellets (m–1),
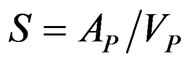
T Temperature (K).
u Velocity of gases (m/hr)
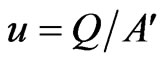
Greek Letters
εB Porocity of packed bed (m3 void/mr3)θ Thiele modules (dimensionless unit).
ηk Reaction effectiveness factor for reaction k (dimensionless unit).
μg Viscosity of gases (Pa.s).
υi Stoichiometric coefficient of i-component in the chemical reactions equations (dimensionless unit).
ρb Bulk density (kg/m3)
ρc Density of catalyst (kgc/mr3)
ρg Density of gases (kg/m3)
Abbreviations
C.D.R. Carbon Dioxide ReformingIN Inlet stream
OUT outlet stream
S.C.F.R.S. State Company of Fertilizers South Region
S.M.R. Steam Methane Reforming
W.G.S. Water Gas Shift
NOTES
*Corresponding author.
No comments:
Post a Comment